The Revolution of Welder Lasers and Laser Cleaners for Rust in the Hardware Industry
The hardware industry is at a crossroads—caught between increasing demand for higher precision, faster production, and a greater need for environmental sustainability. Yet, in this rapidly evolving landscape, a single innovation has emerged as the golden key: welder lasers and laser cleaners for rust. These technologies are not just enhancements; they are transforming the core processes of hardware manufacturing, delivering unparalleled benefits that were previously unattainable.
Imagine this: parts and tools that are welded together with precision, durability, and minimal waste, all while the surfaces remain clean and free from rust—no chemicals, no abrasives, and no harmful emissions. This is no longer a dream but a reality brought about by the integration of welder lasers and laser rust cleaners into hardware production. The hardware industry, traditionally reliant on time-consuming and labor-intensive methods, is now embracing the efficiency, speed, and eco-friendliness offered by these advanced laser technologies.
CQX LASER, a leader in cutting-edge laser solutions, is at the forefront of these innovations, providing hardware manufacturers with the tools to push the boundaries of what’s possible. From automating processes to reducing costs, these technologies are revolutionizing the hardware industry in ways never seen before.
1. The Power of Welder Lasers in Hardware Manufacturing
Laser welding, often referred to as welder lasers, has proven to be a breakthrough technology in the manufacturing sector, particularly within industries that demand precision and durability. Traditional welding methods, though effective, often come with limitations—high heat input, slow processing time, and the risk of distorting delicate materials. Welder lasers eliminate these drawbacks by offering a controlled, focused beam of light that joins materials with high precision and minimal thermal distortion.
Precision and Quality in Every Weld
The key to the success of welder lasers lies in their ability to provide high levels of precision. Unlike conventional welding, where heat is often spread across a wide area, laser welding directs concentrated energy at the welding site, melting only the materials in the immediate vicinity. This means that even the smallest components, such as bolts, gears, and mechanical parts, can be welded together with exceptional accuracy.
For the hardware industry, this precision is invaluable. Tools, machinery components, and industrial equipment need to be assembled with care to ensure they meet stringent quality standards. With welder lasers, manufacturers can achieve flawless joints, ensuring both the aesthetic integrity and structural strength of their products.
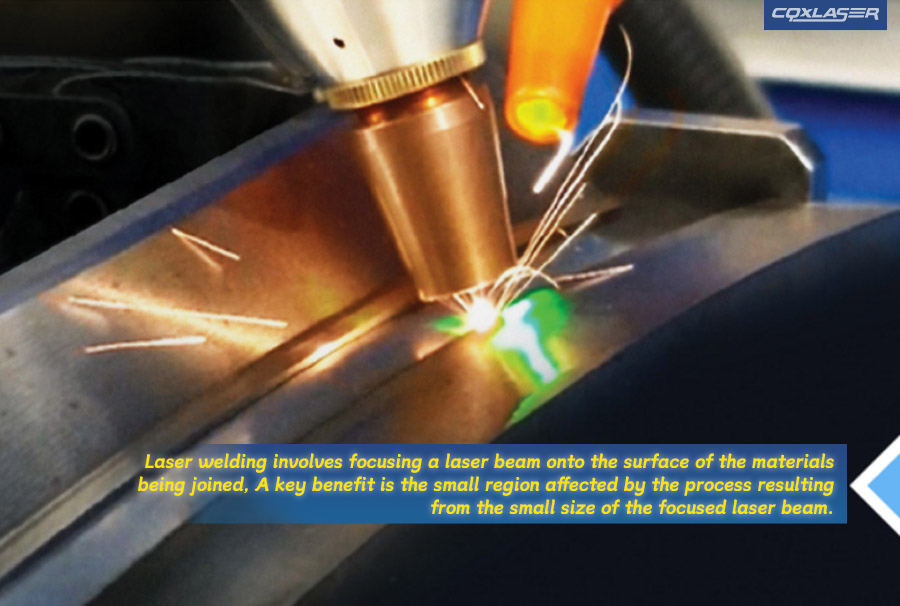
Faster Production, Lower Costs
One of the most significant advantages of laser welding is its ability to speed up production processes. Traditional welding methods often require multiple steps, including the use of filler material and post-weld finishing. In contrast, laser welding reduces the need for filler materials and can be completed in a fraction of the time. This means that hardware manufacturers can produce higher volumes of products in a shorter time frame, ultimately increasing productivity and lowering labor costs.
Additionally, welder lasers minimize material waste. Because the laser beam is so focused, the heat affected zone (HAZ) is smaller, reducing the likelihood of warping or unnecessary material loss. This leads to more efficient use of raw materials and less scrap, providing long-term savings for manufacturers.
Cleaner, Safer Manufacturing Environment
Unlike traditional welding, which can produce harmful fumes, smoke, and sparks, welder lasers operate in a cleaner environment. This is particularly important in industries where worker safety and environmental concerns are top priorities. With welder lasers, the process is significantly cleaner, reducing the need for ventilation systems and safety equipment typically required in conventional welding setups. Furthermore, this reduction in fumes also contributes to the overall health of the workers and lowers the environmental impact of the manufacturing process.
2.Laser Cleaners for Rust: The Future of Surface Treatment
Rust and other forms of corrosion are a major challenge for the hardware industry. Tools, machinery, and structural components exposed to moisture or harsh environments can quickly succumb to rust, leading to degraded performance and a shorter product lifespan. Traditional methods for rust removal, such as sandblasting or chemical cleaning, can be inefficient, messy, and environmentally damaging. Enter laser cleaners for rust—a revolutionary approach to cleaning and rust removal that is taking the hardware industry by storm.
How Laser Cleaning Works
Laser cleaning uses high-intensity laser pulses to remove contaminants, including rust, from metal surfaces. The laser’s energy interacts with the rust or other contaminants, causing them to vaporize or be blown away by the pressure generated by the laser beam. The precision of laser cleaning means that only the rust or unwanted layers are removed, leaving the base metal intact.
For hardware manufacturers, laser cleaners for rust provide a highly effective, efficient, and eco-friendly solution for rust removal. This method is not only faster than traditional cleaning techniques but also offers a higher level of precision, ensuring that the components are cleaned thoroughly without damaging the material underneath.
Eco-Friendly and Cost-Effective
One of the standout benefits of laser rust cleaning is its eco-friendliness. Unlike chemical-based cleaning methods, laser cleaning doesn’t require the use of hazardous substances or abrasive materials. There are no harmful chemicals to dispose of, and no secondary waste is generated in the process. This makes laser cleaning a more sustainable option for manufacturers looking to reduce their environmental footprint.
In addition to being eco-friendly, laser rust cleaners also offer long-term cost savings. Traditional cleaning methods often require expensive chemicals, abrasive materials, and maintenance of equipment like sandblasters. Laser cleaning eliminates the need for these consumables, reducing ongoing operational costs. Moreover, the precision of the laser ensures that cleaning is highly efficient, leading to faster turnaround times and greater throughput.
Improved Durability and Finish Quality
Rust removal is critical not just for aesthetic reasons but also for the longevity and performance of hardware products. Corrosion can weaken metal parts, making them more susceptible to failure. By using laser rust cleaners, manufacturers can restore the integrity of components, ensuring that they are strong, durable, and able to withstand the rigors of their intended use.
Furthermore, laser cleaning provides a clean surface that enhances the adhesion of coatings and finishes. For hardware components that require painting or other protective layers, laser cleaning for rust ensures that the coating bonds more effectively, resulting in a longer-lasting finish that is resistant to wear and corrosion.
3.Integrating Welder Lasers and Laser Rust Cleaners: Optimizing Production Efficiency
The true potential of welder lasers and laser rust cleaners lies in their integration into the production line. By combining these two technologies, manufacturers can streamline their entire workflow, from surface preparation to final assembly.
A Seamless Manufacturing Process
In the hardware industry, ensuring that components are clean and free from contaminants is crucial before any welding takes place. By using laser rust cleaners to prepare the surfaces, manufacturers can ensure that the metal is free from rust, oil, and other impurities that could affect the quality of the weld. After cleaning, the welder lasers can be employed to create precise, strong joints, completing the manufacturing process with minimal waste and maximum efficiency.
This integrated approach not only improves product quality but also increases productivity. With faster processing times, fewer defects, and less post-production work, manufacturers can produce more units in less time, meeting the increasing demand for high-quality hardware products.
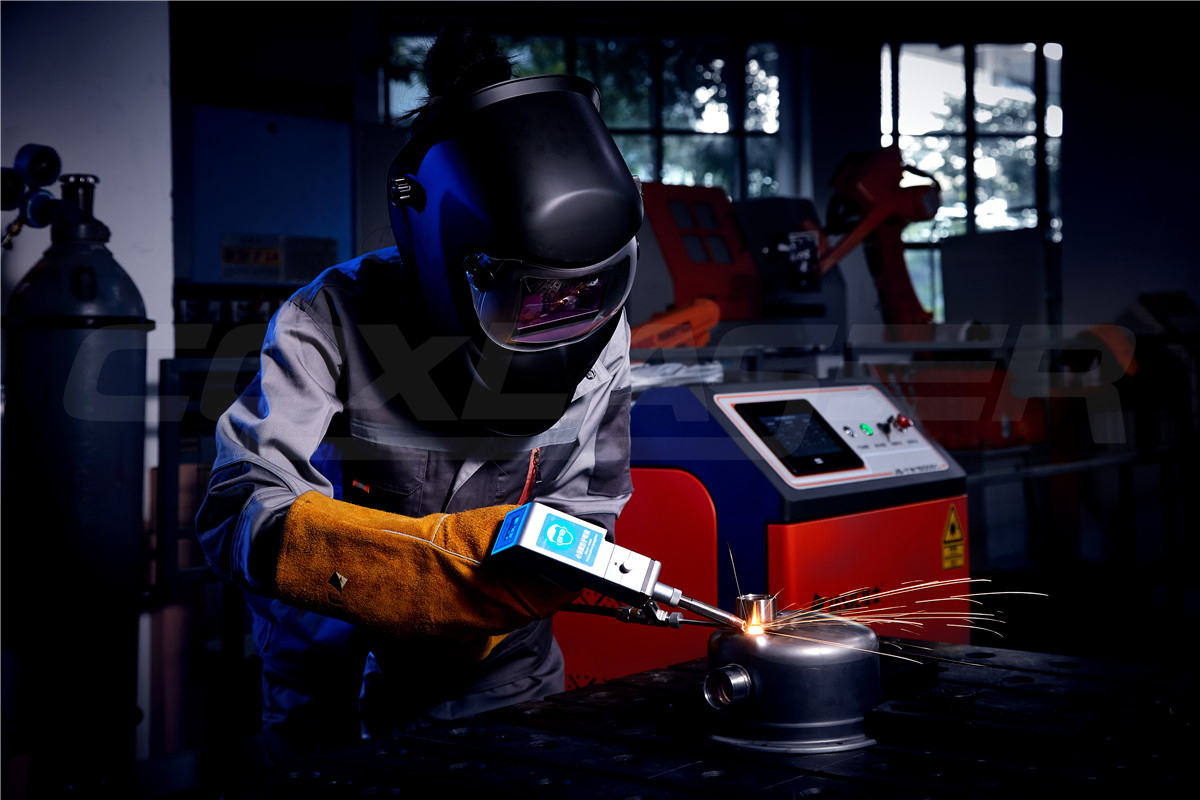
4.Looking Ahead: The Future of Laser Technologies in Hardware Manufacturing
The use of welder lasers and laser cleaners for rust in the hardware industry is just beginning to gain momentum. As the demand for precision, efficiency, and sustainability continues to rise, these technologies will become even more critical to the future of manufacturing.
Manufacturers who adopt these cutting-edge technologies will be better equipped to compete in a rapidly evolving marketplace. By reducing production costs, improving product quality, and adhering to environmental standards, laser solutions are not just transforming the hardware industry—they are shaping its future. As innovations continue to emerge, companies that integrate these technologies will lead the way in producing high-quality, durable, and cost-effective hardware.
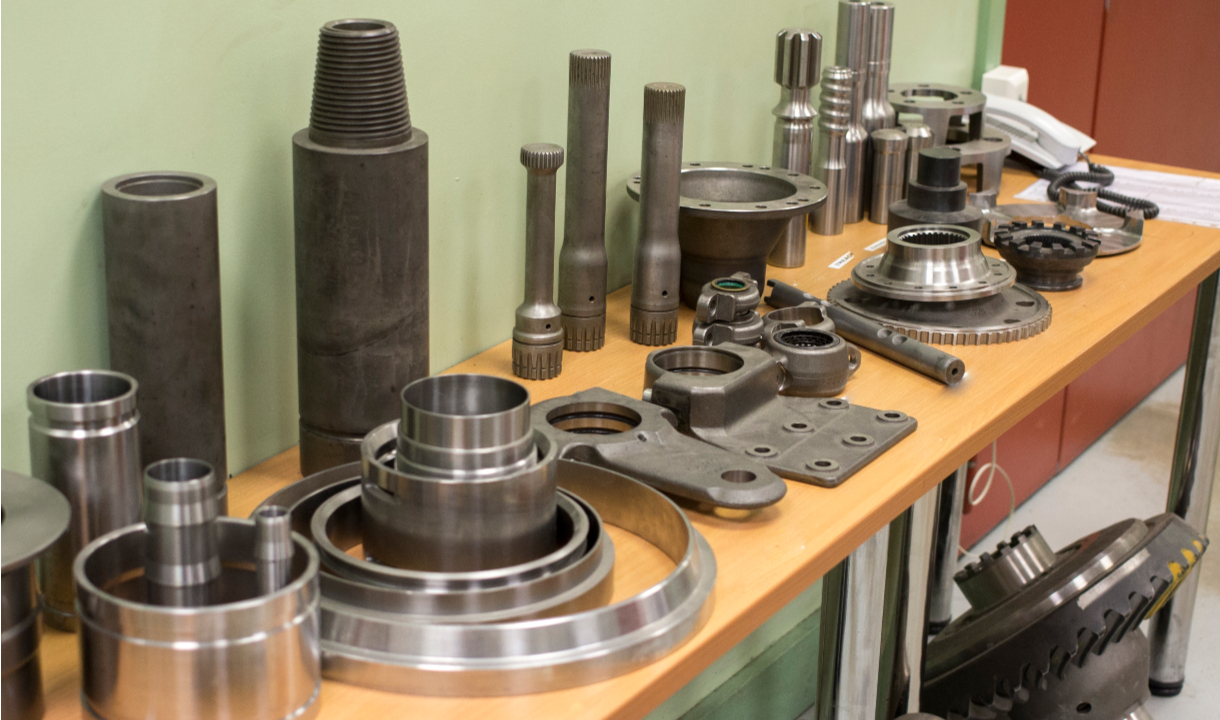