Before using a laser welding machine to weld materials, we need to set the process parameters of the laser welding machine to achieve a more perfect welding effect. The three most important parameters are: speed, power and auxiliary gas.
Welding Speed
Generally speaking, before determining what parameters to choose for a workpiece, the processing speed must be determined first. This requires communication with customers and depends on customer needs. For example, if there are beat requirements and output requirements for production, you can reverse the approximate speed, and then do process debugging on this basis.
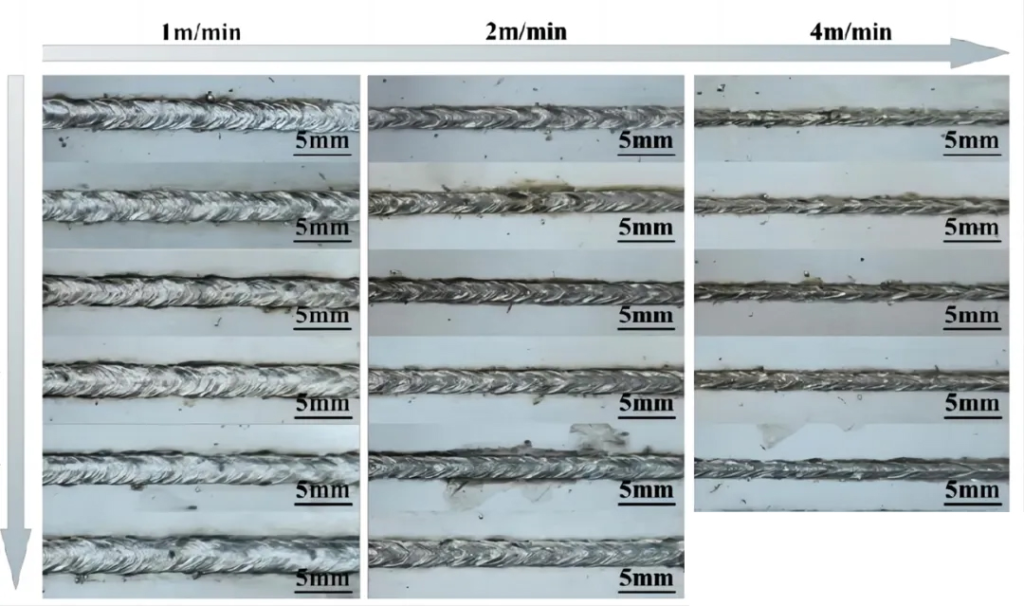
In the laser welding process, the welding speed directly affects the linear energy density of the laser beam, which has a greater impact on the weld size. At the same time, at different welding speeds, the flow form of the molten pool during laser welding is also different.
The core of the law of speed affecting welding is to affect the linear energy distribution and thus affect the laser action time, which in turn leads to changes in metallographic penetration and width. The penetration width decreases with increasing welding speed; the penetration depth decreases with increasing welding speed; speeding up can reduce defects such as undercut and spatter to a certain extent.
Laser Power
Generally speaking: the greater the power, the greater the penetration depth and width. Laser welding has an energy critical point. Below the critical point is thermal conduction welding, and above it is deep penetration welding. Common defects caused by insufficient power are mainly: cold welding, shallow penetration, unclear weld marks; defects caused by excessive power: welding penetration, large spatter, wavy edges, undercuts, etc.
The relationship between power and penetration depth and width: the greater the power, the greater the penetration depth and width.
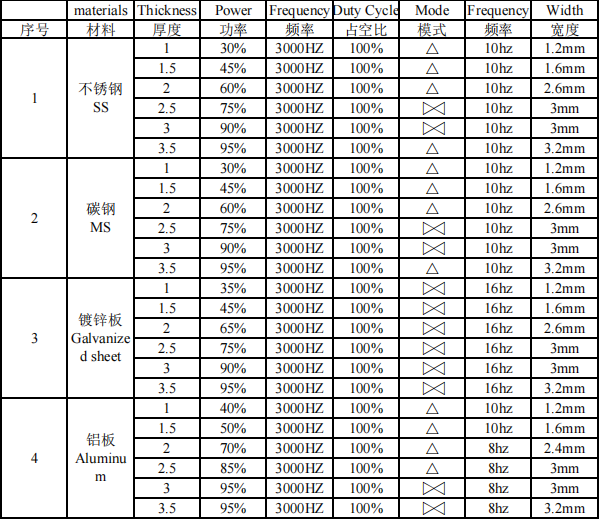
Auxiliary gas
Because the laser welding process is a high-temperature and violent reaction process, the metal melts and evaporates. The metal is extremely active at high temperatures. Once it encounters oxygen, it will react violently, resulting in a large amount of spatter and a rough weld surface. Therefore, the auxiliary gas is used to create an oxygen-free environment in a small range to prevent violent oxidation reactions that cause poor welds and rough appearance.
In industrial production, nitrogen or argon is usually selected.
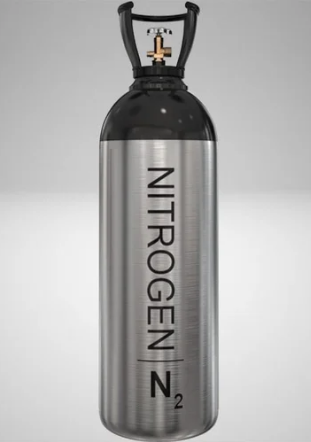