Laser Welder Prices: What You Need to Know Before Investing
A game-changing tool, a marvel of precision, a beacon of industrial evolution—the laser welder is not just a piece of equipment, it is the future of welding technology. But for those stepping into this sophisticated world, there is one major question: What determines laser welder prices? Understanding the costs involved and what influences them is crucial for anyone considering an investment in this cutting-edge technology. Whether you’re a beginner exploring laser welding for the first time or an industry professional looking to expand your capabilities, this guide will help you navigate the many facets of laser welder pricing, ensuring you get the best value for your money.
1. What is a Laser Welder?
1.1 Overview of Laser Welding Technology
Laser welding is a process that uses a focused laser beam to join materials, usually metals, with exceptional precision. The laser beam generates intense heat that melts the materials, allowing them to fuse together seamlessly as they cool. This method is particularly valued for its speed, efficiency, and minimal material distortion.
1.2 Key Features of a Laser Welder
• High Precision: Laser welders are capable of creating extremely accurate and clean welds, making them suitable for delicate and high-value applications.
• Speed: The ability to rapidly heat and weld materials makes laser welding faster than many traditional welding methods.
• Versatility: Laser welders can handle a wide range of materials and welding scenarios, from ultra-thin metals to more substantial pieces.
2. Key Factors Influencing Laser Welder Prices
2.1 Laser Type
The type of laser used—such as fiber, CO₂, or diode—is a primary factor affecting the cost of a welder. Fiber lasers are often more expensive than CO₂ lasers because they offer higher efficiency, better beam quality, and reduced maintenance needs. Fiber lasers are ideal for most industrial applications, while CO₂ lasers are more suited for non-metallic materials.
2.2 Power Output
The power output of a laser welder directly influences its price. Higher power levels allow the welder to penetrate thicker materials and weld more quickly, but they also increase the cost of the machine. Lower power models may be sufficient for tasks involving thin or delicate materials, whereas industrial applications often require higher wattage to achieve optimal welds.
2.3 Cooling System
Effective cooling is crucial for maintaining performance, especially during extended welding operations. Systems with water cooling tend to be more efficient but also more expensive compared to air-cooled systems. Water-cooled welders are better suited for high-power applications that require continuous use.
2.4 Automation and Software Features
Laser welders equipped with advanced automation, such as programmable settings, integrated cameras, and precision-guided software, command higher prices.
These features, however, enhance productivity, reduce human error, and are particularly valuable for large-scale manufacturing.
2.5 Build Quality and Durability
The materials and construction quality of the laser welder significantly impact its price. A well-built machine designed for longevity, using high-quality components, will naturally be more expensive but offer better long-term value. CQX welders, for instance, prioritize durability and quality, making them a preferred choice for reliability.
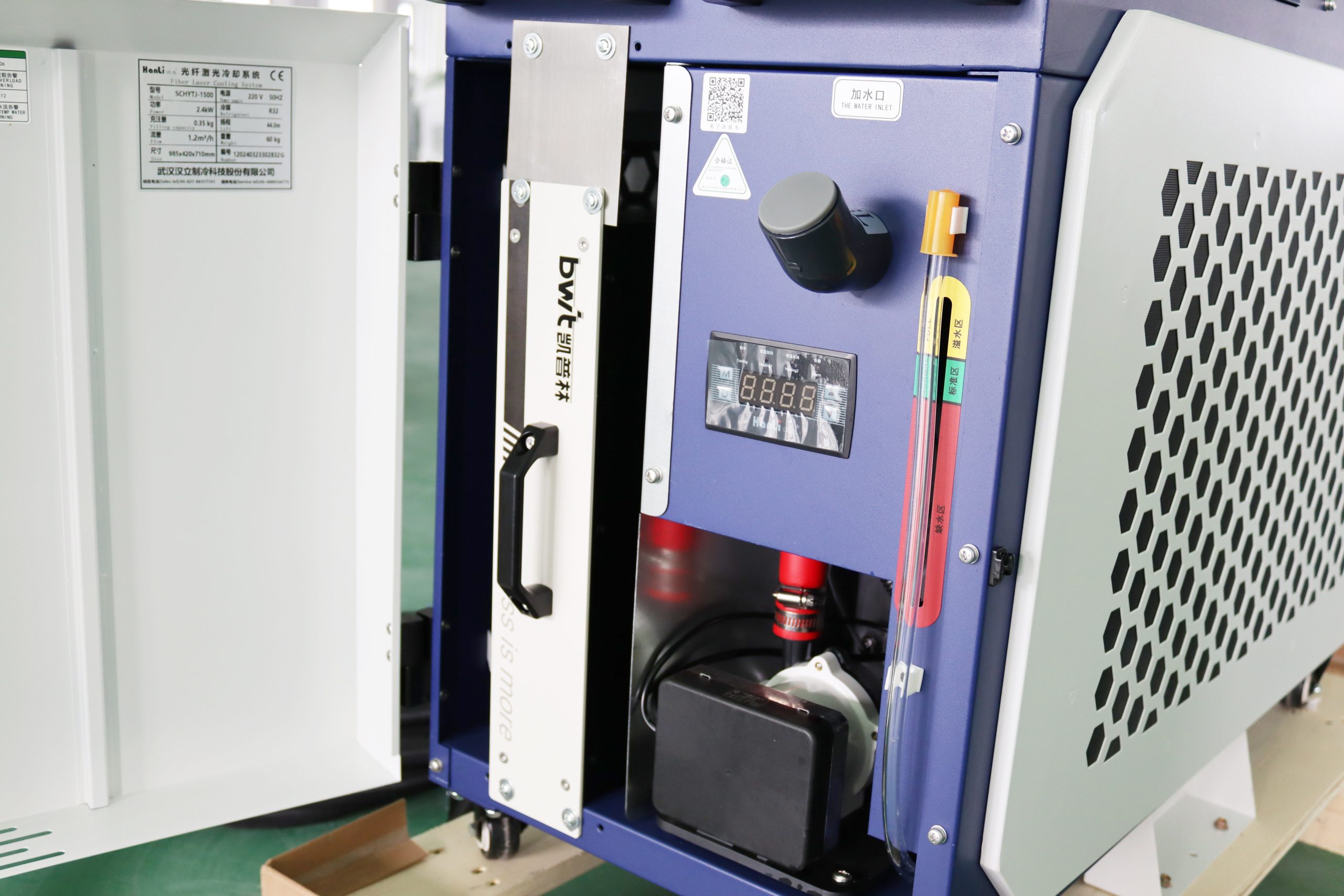
3. Price Categories for Laser Welders
3.1 Entry-Level Laser Welders
• Price Range: $4,000 to $10,000
• Use Cases: Suitable for hobbyists, small businesses, or workshops requiring light welding tasks.
• Features: Typically feature lower power output and fewer automated functions, focusing on basic usability and reliability for small projects.
3.2 Mid-Range Laser Welders
• Price Range: $10,000 to $30,000
• Use Cases: Ideal for medium-sized businesses needing higher power and more versatility.
• Features: Includes advanced cooling systems, moderate power output, and some automated features that improve accuracy and efficiency.
3.3 High-End Laser Welders
• Price Range: $30,000 to $100,000+
• Use Cases: Designed for industrial and specialized applications where precision and power are critical.
• Features: High-power output, full automation capabilities, and advanced safety features. These machines are suitable for continuous, high-volume operations.
4. Balancing Cost and Value in Laser Welders
4.1 Evaluating Long-Term Return on Investment (ROI)
When considering laser welder prices, it’s crucial to look beyond the initial cost and evaluate the long-term ROI. A higher-priced laser welder, such as those offered by CQX, can offer substantial savings over time through increased productivity, lower maintenance costs, and reduced waste.
4.2 Maintenance Costs and Durability
While cheaper models may seem appealing, they often come with higher maintenance costs and shorter lifespans. Investing in a durable, high-quality laser welder can reduce downtime and costly repairs, ultimately providing better value for money.
4.3 Energy Efficiency
Energy consumption is another critical factor. Laser welders are generally more energy-efficient than traditional welding methods, but models with advanced energy-saving features can further lower operational costs, especially in high-production environments.
5. Key Applications and Their Cost Implications
5.1 Automotive Manufacturing
Laser welders are extensively used in the automotive industry for tasks like welding car bodies, exhaust systems, and battery packs. High precision and speed reduce production time, which is critical for mass production. For automotive manufacturers, investing in a higher-end laser welder can pay off significantly through faster cycle times and reduced defect rates.
5.2 Aerospace and Defense
In aerospace, the ability to create strong, precise welds with minimal material stress is crucial. The higher costs of specialized laser welders are justified by the need for superior quality and safety in welded components.
5.3 Medical Device Production
Laser welding is used in the medical industry for creating devices that require sterile and highly precise welds, such as surgical tools and implants.
The cost of a laser welder for medical applications often reflects the additional requirements for accuracy and compliance with strict safety standards.
5.4 Jewelry and Electronics
For delicate applications, such as jewelry and small electronic components, laser welders offer unmatched precision.
Entry to mid-range welders are often sufficient for these applications, providing a balance between cost and functionality.
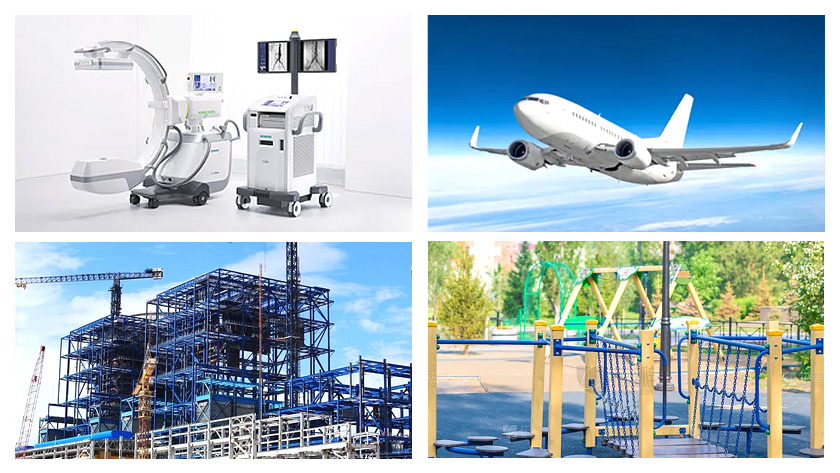
6. How CQX Laser Welders Stand Out
6.1 Innovative Technology for Optimal Performance
CQX laser welders incorporate cutting-edge technology to provide reliable and precise welding solutions. With advanced features such as real-time monitoring and customizable welding parameters, CQX welders are designed for a wide range of applications, ensuring users get the best value for their investment.
6.2 Durability and Robust Design
Built with high-quality materials, CQX welders are engineered for durability and long-term use. This reduces the need for frequent replacements and repairs, helping businesses save money in the long run.
6.3 Comprehensive Customer Support
CQX offers extensive support, including training programs and maintenance services, ensuring that users can operate their machines effectively and extend their lifespan. This after-sales support is an essential factor to consider when evaluating the true cost of a laser welder.
7. Future Trends Influencing Laser Welder Prices
7.1 Automation and Artificial Intelligence
As automation and AI become more integrated into laser welding technology, the upfront cost of laser welders is likely to increase. However, these technologies will lead to greater efficiency, reduced labor costs, and improved quality, ultimately making them a cost-effective option in the long term.
7.2 Portable and Compact Designs
The demand for portable laser welders is rising, particularly for on-site applications. As technology advances, the price for portable models with higher power output and enhanced features may decrease, making them more accessible for various industries.
7.3 Sustainable Manufacturing Solutions
With increasing focus on sustainability, laser welders that are energy-efficient and minimize waste will be more in demand. Future developments will likely bring about innovations that improve energy efficiency, which could influence pricing trends.
8. Practical Tips for Choosing a Laser Welder
8.1 Assessing Your Welding Needs
Understanding the specific requirements of your projects—such as material type, thickness, and production volume—will help you determine the appropriate laser welder. This assessment ensures that you do not overspend on unnecessary features.
8.2 Comparing Features vs. Price
When comparing laser welder prices, consider the features included. Automation capabilities, cooling systems, power output, and software features all impact the machine’s efficiency and usability.
8.3 Considering Long-Term Support
The quality of after-sales support is crucial. A laser welder is a significant investment, and partnering with a brand like CQX, which offers comprehensive support and maintenance services, ensures your machine remains in optimal condition, maximizing its value.
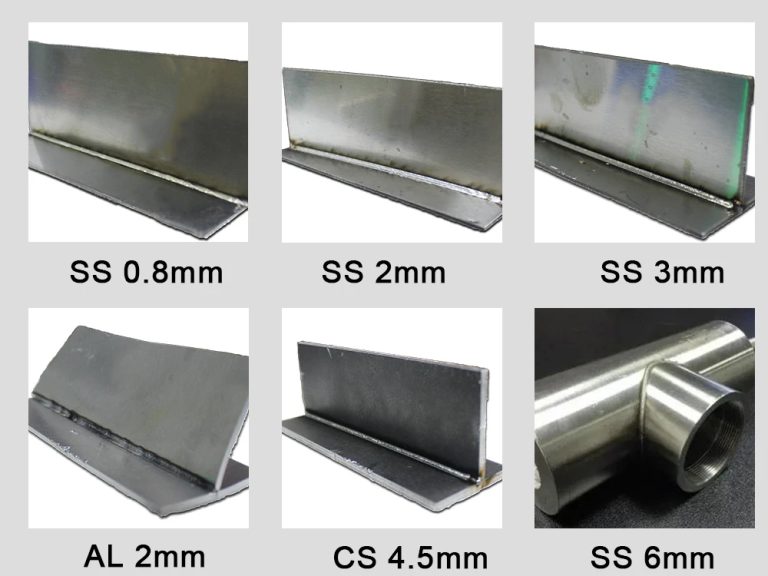
The world of laser welder prices can be complex, with numerous factors influencing the cost of these sophisticated machines. From understanding different price categories and their features to assessing long-term value and industry applications, making an informed decision is key to finding the right welder for your needs. CQX stands out in providing innovative, durable, and cost-effective laser welding solutions that cater to a wide array of industrial requirements. By considering the factors discussed in this guide, you can confidently navigate the laser welding market and choose a machine that aligns with your specific goals and budget.