Laser Welder Price: Decoding the Cost of Precision and Innovation
Price tags often spark curiosity, especially when they’re tied to cutting-edge technology. But a laser welder price is more than just a number—it reflects the craftsmanship, precision, and innovation that shape modern industries. Whether you’re a small business owner exploring investment options or a seasoned manufacturer seeking the perfect welding solution, understanding what influences the cost of laser welders can be your key to making an informed decision. This guide unpacks everything you need to know, from pricing trends and value-for-money considerations to how CQX delivers unparalleled solutions in the laser welding market.
1. The Components of Laser Welder Pricing
1.1 The Basics Behind the Cost
The price of a laser welder is determined by several technical and operational factors. A basic handheld laser welder starts at a lower range, while high-powered industrial models can cost significantly more.
Key pricing drivers include:
• Laser Type: Fiber lasers typically cost more than CO2 lasers due to their precision and efficiency.
• Power Output: Higher power equates to deeper and faster welds but comes with a heftier price tag.
• Customization Options: Machines tailored to specific tasks often command a premium.
1.2 Research and Development Costs
The cutting-edge nature of laser technology means manufacturers invest heavily in research and development, pushing up the cost of high-quality laser welders.
2. Understanding the Different Price Ranges
2.1 Entry-Level Welders
These models are ideal for beginners or small-scale projects.
• Price Range: $5,000–$15,000
• Capabilities: Basic welding tasks on thin materials.
2.2 Mid-Range Welders
Designed for businesses needing advanced features without breaking the bank.
• Price Range: $15,000–$50,000
• Capabilities: Higher power and versatility for medium-sized projects.
2.3 High-End Industrial Welders
Top-tier options for large-scale manufacturing.
• Price Range: $50,000–$500,000+
• Capabilities: Advanced automation, deep weld penetration, and rapid operation.
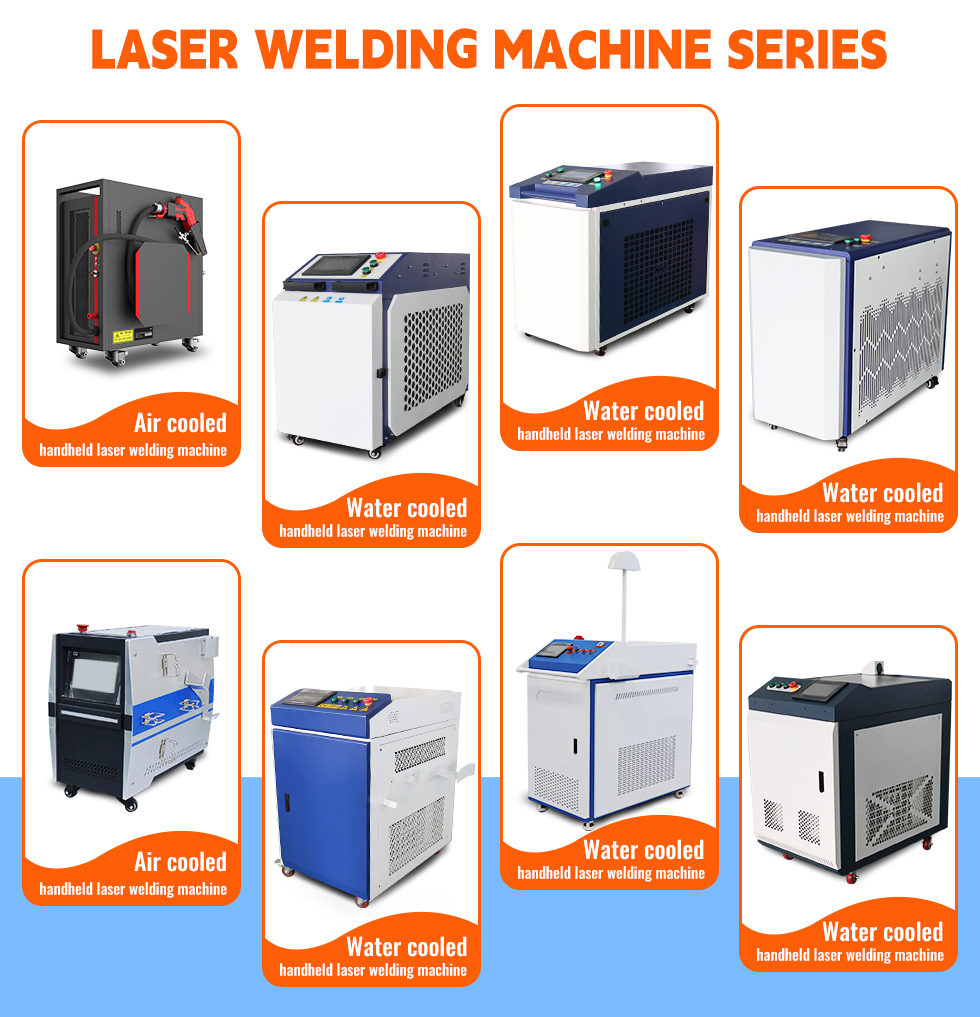
3. Factors Influencing Laser Welder Prices
3.1 Laser Technology Type
• Fiber Lasers: High precision, low maintenance, higher cost.
• CO2 Lasers: Basic welding tasks on thin materials.
• Diode Lasers: Compact and cost-efficient but less powerful.
3.2 Power and Beam Quality
Power output and beam quality directly affect welding speed and precision. Higher specifications lead to better results but increase the price.
3.3 Cooling Mechanisms
Sophisticated cooling systems enhance longevity but add to upfront costs.
3.4 Automation and AI Integration
Welders with built-in AI or automation features offer exceptional efficiency at a premium price.
3.5 Material Compatibility
Machines designed to handle diverse materials, including high-reflectivity metals like copper and aluminum, tend to cost more.
4. Are Higher-Priced Laser Welders Worth It?
4.1 Long-Term Savings
Although a high-end laser welder might seem expensive initially, it often leads to long-term savings through:
– Reduced material waste.
– Faster production times.
– Minimal maintenance requirements.
4.2 Increased Capabilities
A pricier machine often provides:
– Greater precision.
– Compatibility with a wider range of materials.
– Advanced features like real-time defect detection.
5. Balancing Cost and Value
5.1 When to Choose an Entry-Level Model
Small workshops or hobbyists can opt for entry-level models to balance affordability with functionality.
5.2 Scaling with Mid-Range Models
Businesses expanding their operations can invest in mid-range models for increased versatility.
5.3 Industrial Giants and High-End Solutions
Large-scale manufacturers benefit from high-end systems capable of handling complex projects efficiently.
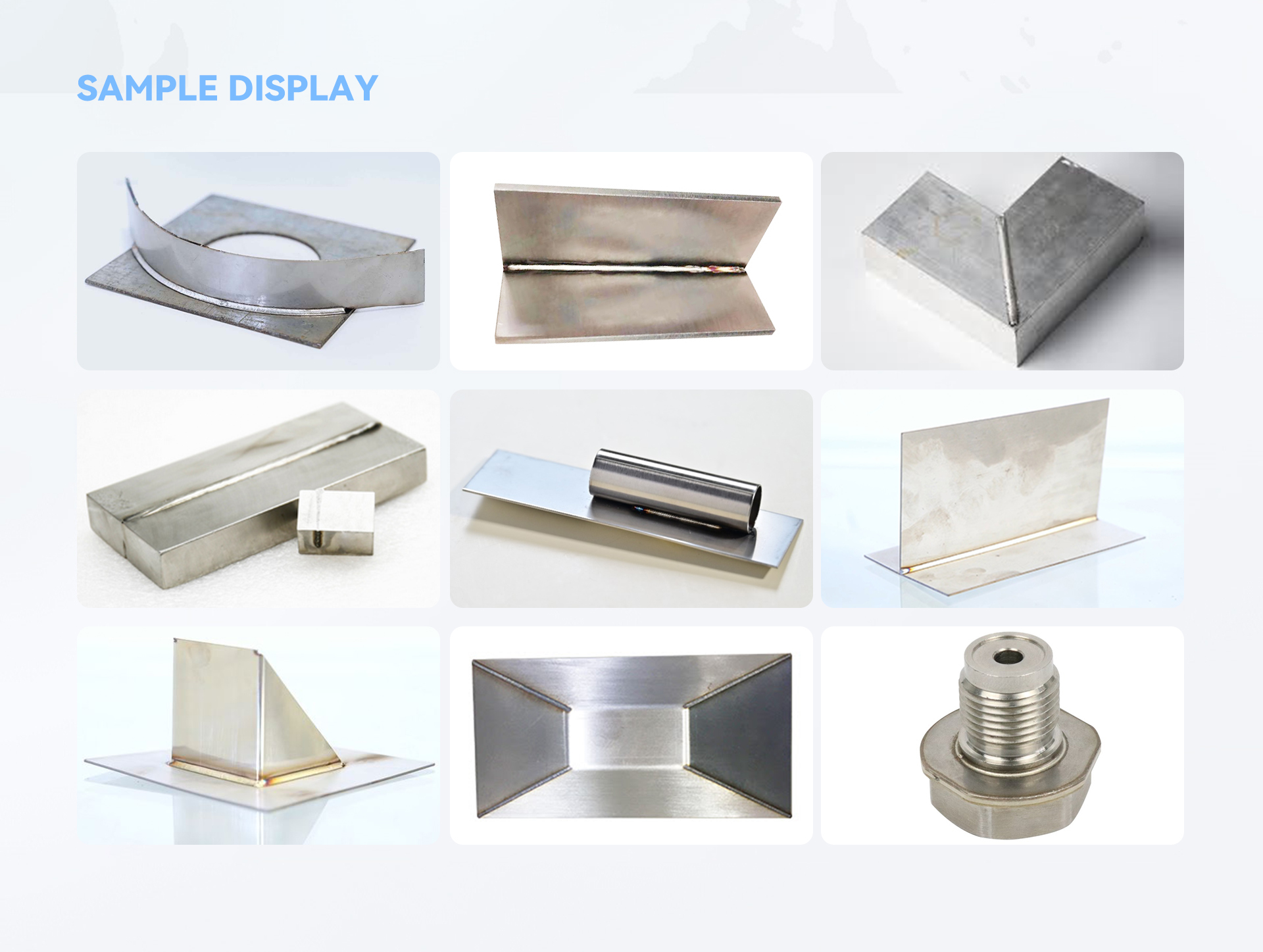
6. How CQX Balances Quality and Affordability
6.1 Innovative Engineering
CQX combines cutting-edge research with practical designs, ensuring their machines deliver exceptional performance without unnecessary costs.
6.2 Comprehensive Support
Investing in CQX systems means access to robust warranties and expert support, maximizing the value of your purchase.
7. Tips for Buyers: Getting the Best Deal
7.1 Research and Compare
Compare features and prices across multiple suppliers. Look for user reviews and real-world case studies.
7.2 Factor in Operational Costs
Beyond the purchase price, consider long-term expenses like maintenance, power consumption, and replacement parts.
7.3 Timing Matters
Certain times of the year, such as industry expos or end-of-financial quarters, might offer better deals.
8. Maintenance Costs and Their Impact on Overall Price
8.1 Routine Maintenance
Regular cleaning and calibration can extend the lifespan of your welder.
8.2 Spare Parts
High-quality welders typically require fewer replacements, reducing operational costs over time.
9. Innovations Driving Future Pricing Trends
9.1 AI and Machine Learning
As AI becomes more integrated into welding machines, costs may rise initially but drop as technology matures.
9.2 Energy Efficiency
The industry is shifting toward greener solutions, potentially influencing prices.
9.3 Modular Designs
Future laser welders may offer customizable modules, allowing businesses to upgrade without replacing entire systems.
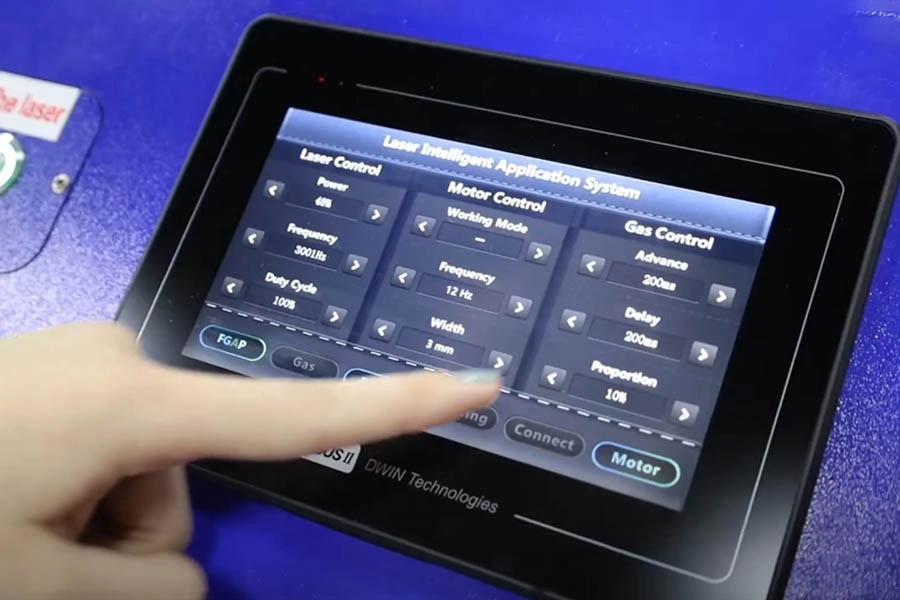
10. Key Takeaways for Buyers
Laser welder prices reflect the intricate balance of precision, technology, and application-specific features. From understanding the different price ranges to exploring how CQX provides value-driven solutions, this guide equips you with the knowledge to make a confident investment. Whether you prioritize portability, power, or advanced automation, aligning your choice with your unique needs will ensure you reap the full benefits of laser welding technology.