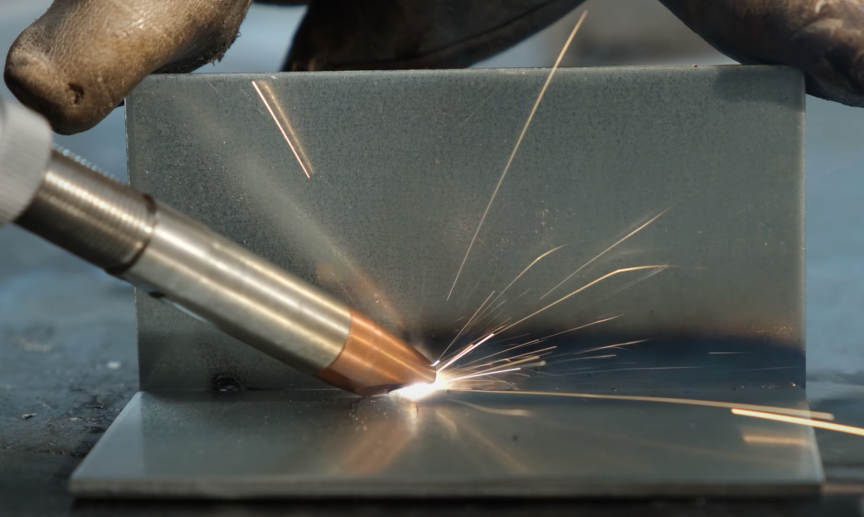
How Much is a Laser Welder? An In-Depth Cost Analysis
When it comes to welding, precision and efficiency matter. The question “how much is a laser welder?” isn’t as straightforward as comparing simple price tags. Laser welders come in a variety of models, each designed for specific applications, from DIY hobbyists to large-scale industrial manufacturers. In this extended guide, we will explore every angle related to laser welder pricing—ranging from the types and features to additional expenses and future trends.
1. A Comprehensive Overview of Laser Welders
1.1 What is a Laser Welder?
A laser welder uses a focused laser beam to join metal or thermoplastics. Unlike traditional welding methods such as TIG, MIG, or arc welding, laser welding provides:
• High precision and minimal distortion
• Fast operation speeds
• Minimal maintenance and post-weld finishing
Laser welders are used across industries such as aerospace, medical, electronics, and jewelry due to their ability to deliver clean, repeatable, and accurate welds.
1.2 Types of Laser Welders
1.Handheld Laser Welders: Portable, easy-to-operate machines used for small to medium tasks.
2.Benchtop Laser Welders: Compact systems ideal for precision applications like jewelry and electronics.
3.Industrial Robotic Laser Welders: High-capacity automated systems designed for production lines.
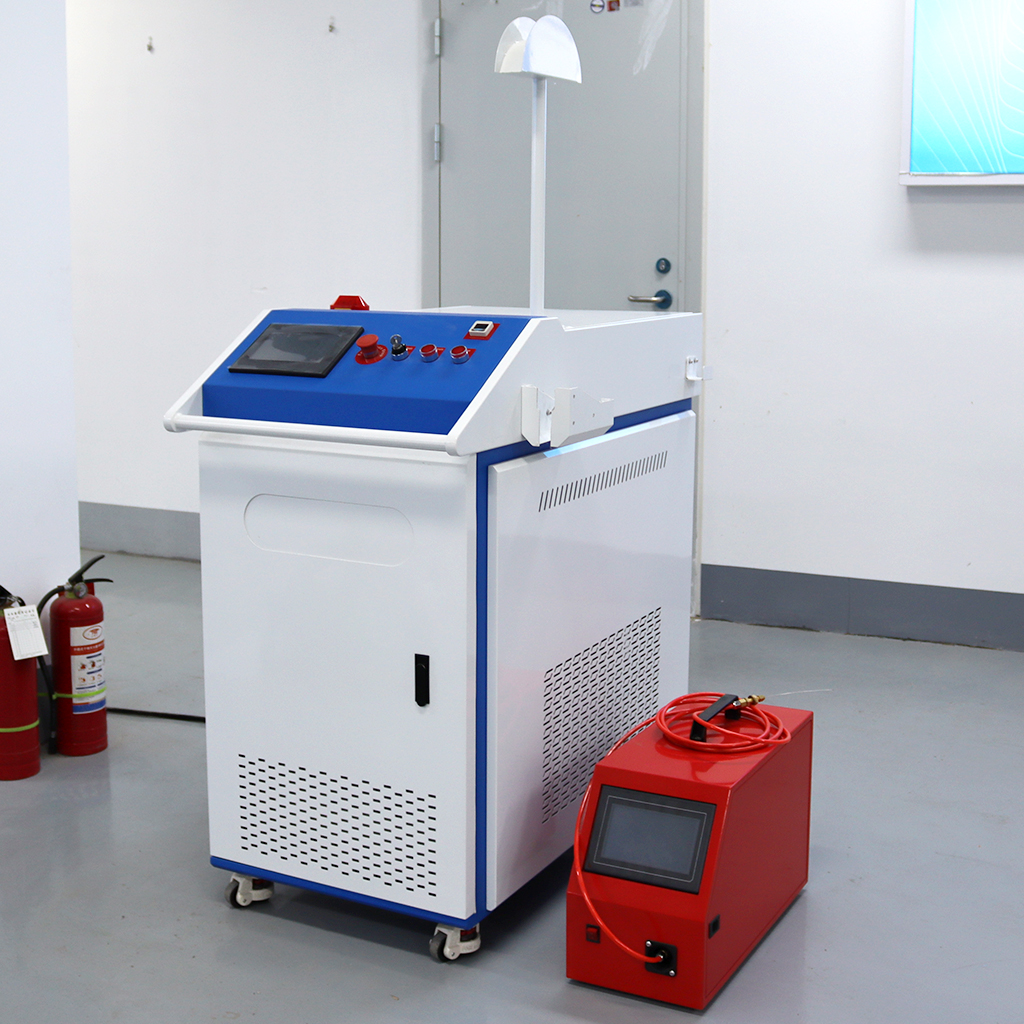
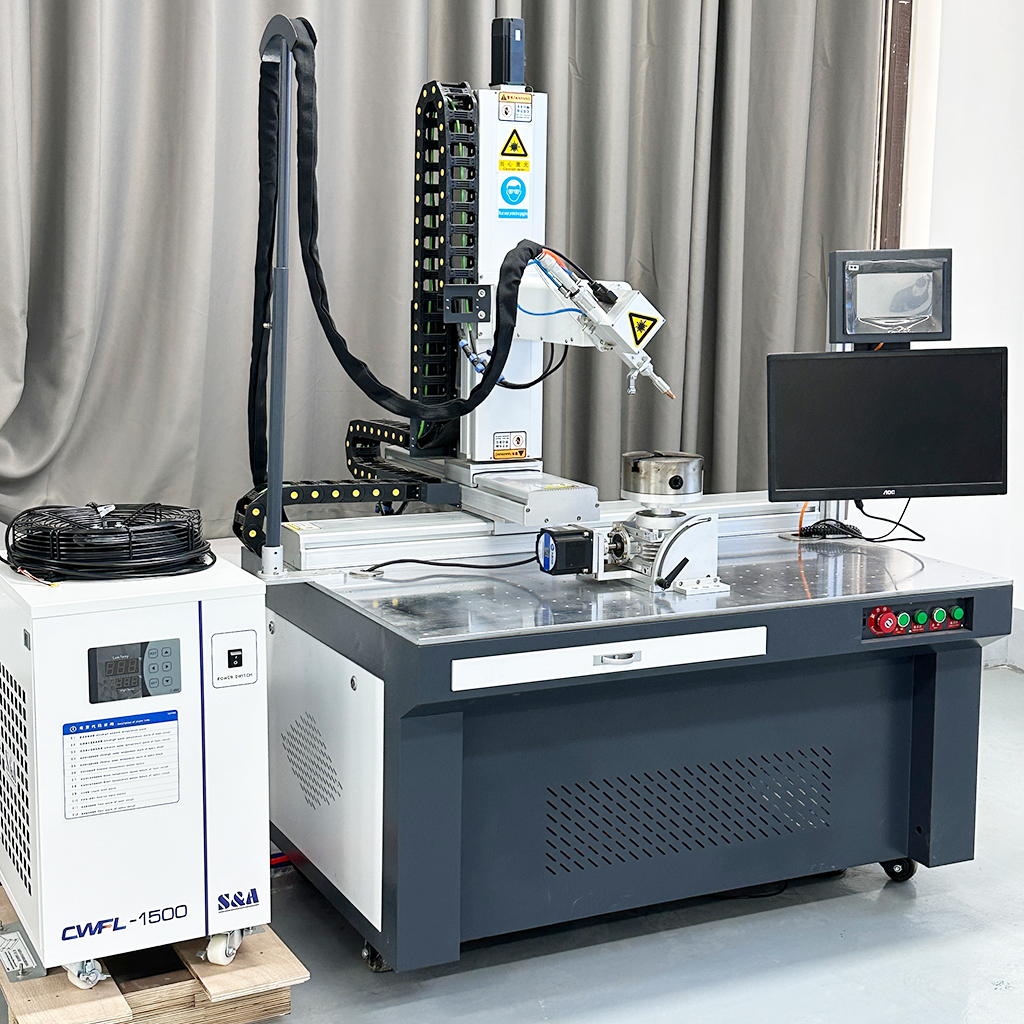
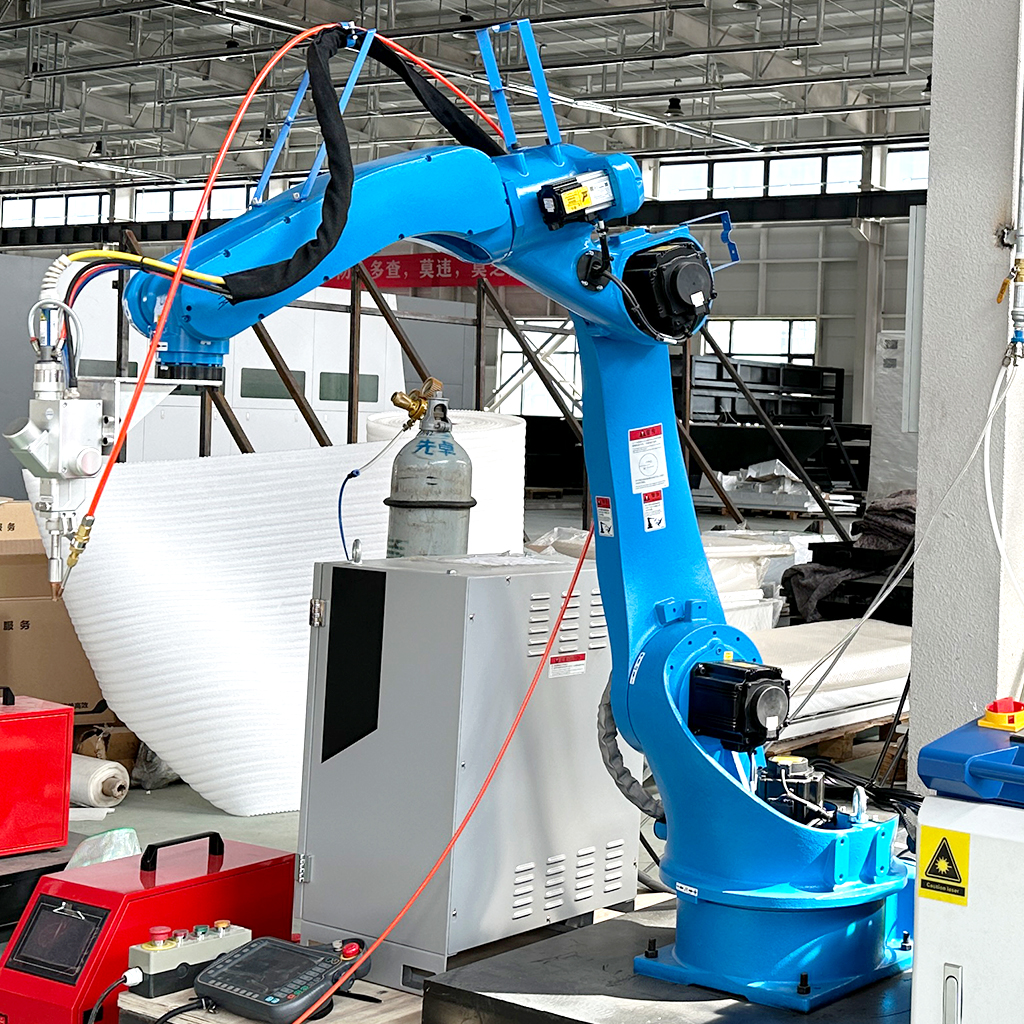
2. Handheld Laser Welders: Affordability Meets Flexibility
Handheld laser welders have transformed welding by making the technology accessible and user-friendly. These machines can handle various materials and are ideal for workshops and small production.
• Typical Price Range:$8,000 – $20,000
• Applications:Sheet metal fabrication, automotive repairs, and furniture assembly
Key Features:
• Simple user interface for faster setup
• Lightweight for portability
• Often water-cooled for longer usage sessions
3. Industrial Laser Welders: High Precision at a Price
For large-scale manufacturing, industrial laser welders are indispensable due to their power and advanced automation features.
• Typical Price Range:$50,000 – $500,000+
• Applications:Aerospace, automotive, and medical device production
Key Features:
• Multi-axis robotic arms for complex welding paths
• Higher wattage options (up to 6,000W)
• Customizable software integration for precision control
4. Factors That Influence the Cost of a Laser Welder
4.1 Wattage Output
The wattage of the laser dictates how much energy it can deliver and how deep it can weld.
• Low Power (100W-500W):Great for delicate welding tasks
• Mid-Range Power (1,000W-2,000W):Suitable for metal sheets and moderate workloads
• High Power (3,000W+):Handles heavy-duty industrial tasks
4.2 Cooling System
• Air-Cooled Systems:Cheaper but less effective for continuous high-power usage
• Water-Cooled Systems:More expensive but highly efficient for long welding sessions
4.3 Automation Level
Manual systems cost significantly less than automated robotic systems, which can increase costs exponentially due to added sensors, software, and calibration requirements.
5. Comparing Laser Welding with Traditional Welding
To understand the value of a laser welder, consider how it stacks up against conventional welding methods.
Welding Method | Initial Cost | Speed | Precision | Post-Processing |
---|---|---|---|---|
TIG Welding | $2,000 - $10,000 | Moderate | High | Frequent |
MIG Welding | $1,500 - $8,000 | Fast | Medium | Minimal |
Laser Welding | $8,000 - $500,000 | Very Fast | Very High | Rare |
Laser welding offers unmatched precision and significantly reduces the need for post-weld finishing, making it a cost-effective solution over time despite the upfront investment.
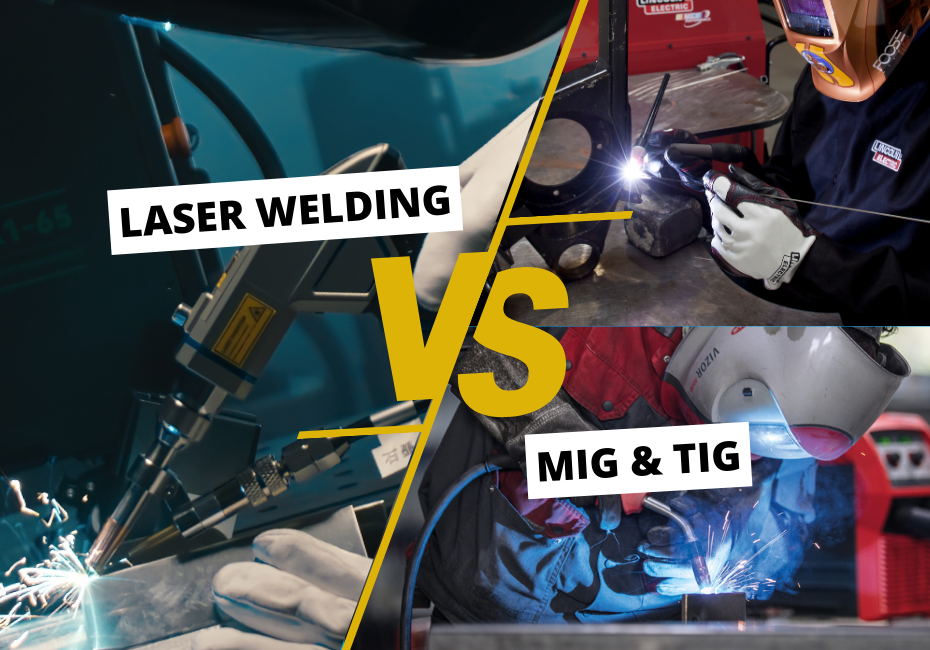
6. Hidden Costs to Factor In
While the upfront cost of a laser welder is a primary consideration, there are other expenses to keep in mind:
• Installation Fees:Some manufacturers offer free installation, while others charge an additional $1,000-$5,000 for setup and testing.
• Maintenance Costs:Although minimal, replacement parts like laser lenses and nozzles may cost between $200-$1,500 annually.
• Software Licenses:Advanced welders with proprietary software may require periodic updates costing $500-$1,000.
• Training:Operator training costs can range from $500 to $5,000, depending on the complexity of the machine.
7. Financing Options for Laser Welders
1.Leasing:Many suppliers offer leasing agreements, allowing companies to pay in monthly installments rather than upfront.
2.Payment Plans:For smaller-scale businesses, staggered payment plans are a feasible way to acquire high-performance equipment.
8. Tips for Choosing the Right Laser Welder
1.Define Your Welding Needs:Consider the type of materials and joint requirements you work with regularly.
2.Evaluate After-Sales Support:Ensure the manufacturer offers robust support, including warranties and access to service centers.
3.Test the Equipment:Request demos to gauge the ease of use and overall performance.
4.Consider Future Scalability:Opt for machines with upgradeable features if you plan to expand production.
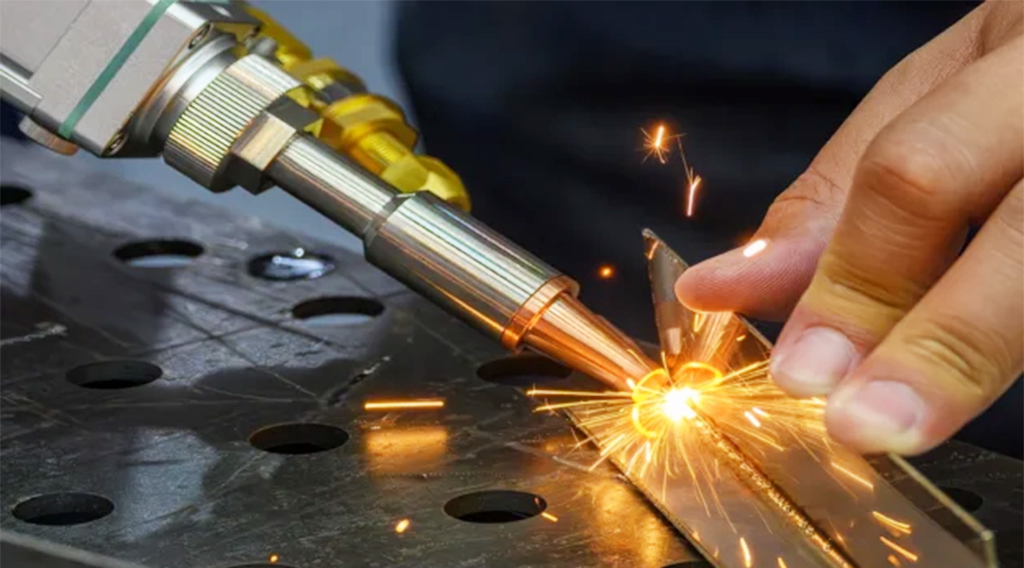
9. Emerging Trends in Laser Welding Technology
• AI-Assisted Welding:Artificial intelligence is being integrated into laser welders to automate defect detection and optimize weld paths in real time.
• Portable Laser Welders:The development of compact, battery-powered laser welders offers greater mobility for fieldwork.
• Sustainability Innovations:Many manufacturers are focusing on energy-efficient models that consume less power without compromising performance.
10. Common FAQs About Laser Welder Pricing
Q: Are there government grants for purchasing laser welders?
A: Yes, in some regions, government programs offer tax incentives and grants for upgrading to energy-efficient equipment.
Q: Can handheld laser welders handle thick materials?
A: Handheld models with 1,000W+ power can handle metal sheets up to 5mm thick.
Q: How long does a laser welding machine last?
A: With proper maintenance, most laser welders last 10-15 years or more.
Laser welders represent a significant investment, but their speed, precision, and versatility can drive operational efficiencies that justify the cost.
By understanding the factors that affect their pricing and identifying your specific needs, you can choose the perfect laser welder for your applications.