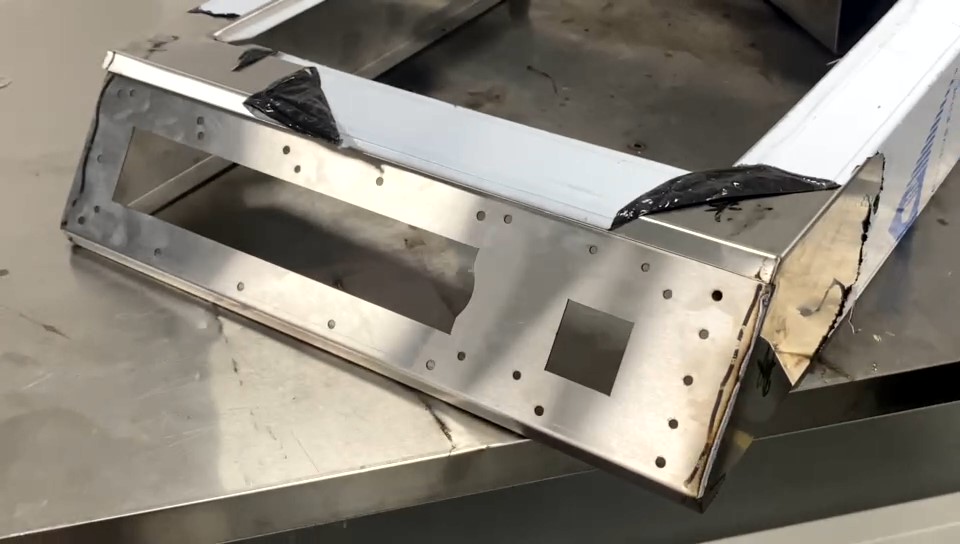
The Ultimate Guide to Laser Weld Aluminum: Precision, Speed, and Innovation
In the fast-evolving world of manufacturing and metalwork, laser weld aluminum stands out as a game-changing technique. Aluminum, prized for its lightweight strength and versatility, poses unique challenges when it comes to welding. Enter laser welding—a method that overcomes these hurdles with precision, speed, and reliability.
This comprehensive guide explores how laser weld aluminum reshapes industries, enhances productivity, and sets new standards for quality.
What is Laser Weld Aluminum?
Laser weld aluminum refers to the process of using a focused laser beam to join aluminum parts. The technology ensures deep penetration and minimal distortion, achieving seamless welds that traditional methods often struggle to match.
Key attributes of laser welding aluminum include:
• Pinpoint accuracy for clean joints.
• Minimal heat-affected zones (HAZ) to preserve material properties.
• High-speed operation for increased productivity.
These benefits make it an ideal choice for industries ranging from aerospace to consumer electronics.
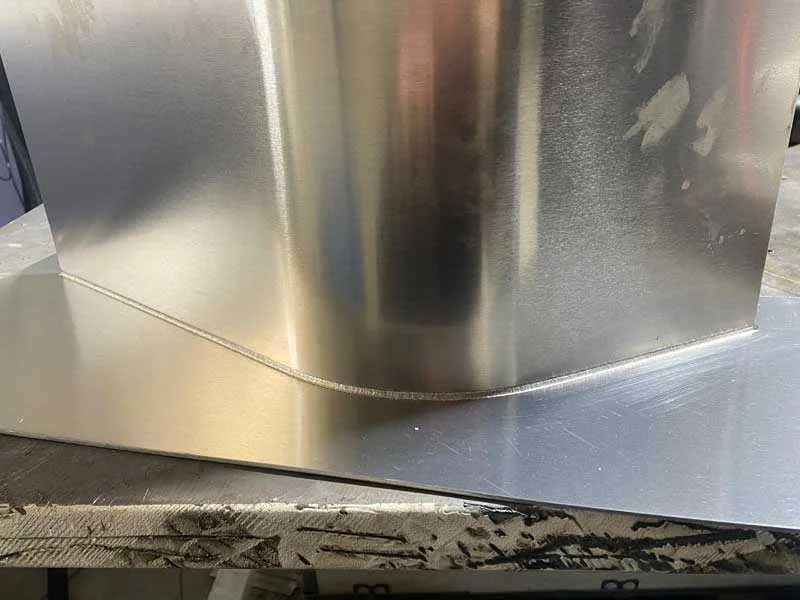
Why Aluminum Welding Requires Specialized Techniques
Unique Properties of Aluminum
Aluminum’s lightweight nature and high thermal conductivity present specific challenges:
1. Oxide Layer: Aluminum forms an oxide layer that must be removed for successful welding.
2. High Reflectivity: Its surface reflects heat, requiring powerful and precise lasers.
3. Thermal Expansion: Aluminum expands significantly when heated, increasing the risk of distortion.
How Laser Welding Overcomes These Challenges
Laser welding mitigates these issues by delivering concentrated energy to the weld joint, reducing heat spread and ensuring consistent results.
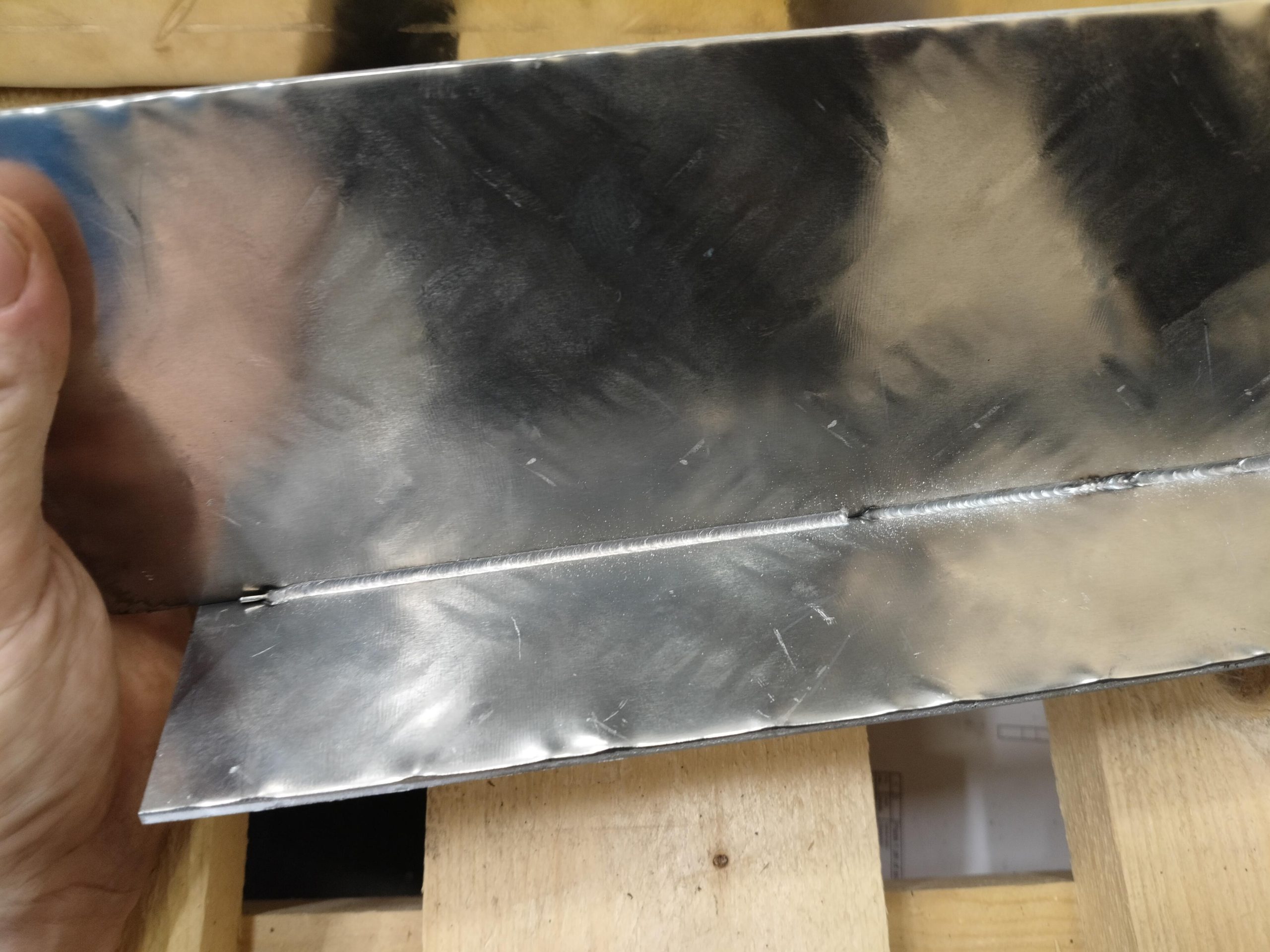
Advantages of Laser Weld Aluminum
1. Superior Weld Quality
Laser welding produces defect-free, aesthetically pleasing joints with minimal porosity and spatter.
2. High Efficiency
The speed of laser welding reduces production times, allowing for quicker turnaround in manufacturing processes.
3. Versatility
Laser welding can handle thin sheets, thick plates, and even dissimilar materials, offering unmatched flexibility.
4. Cost-Effectiveness
Reduced waste, lower energy consumption, and minimal post-weld processing translate to significant cost savings over time.
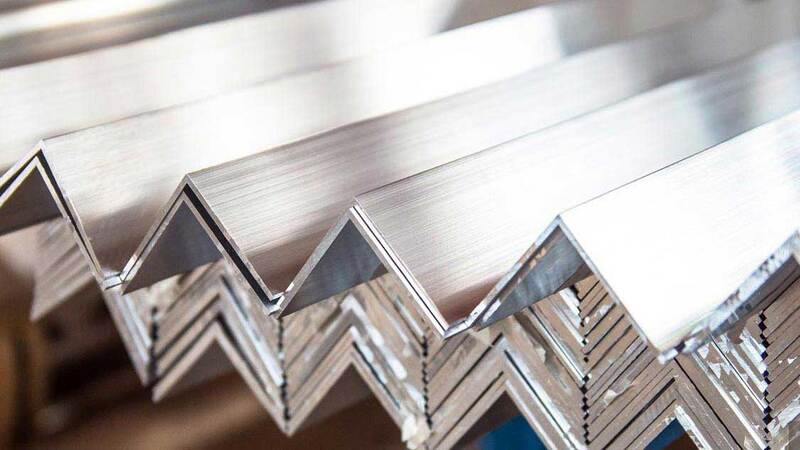
Applications of Laser Weld Aluminum
1. Aerospace and Aviation
In aerospace engineering, aluminum is a cornerstone material for its strength-to-weight ratio. Laser welding ensures high-precision joints for critical components like fuselage panels and wing structures.
2. Automotive Manufacturing
From lightweight car frames to intricate battery casings for electric vehicles, laser welding enhances strength and durability in automotive applications.
3. Consumer Electronics
Smartphones, laptops, and other gadgets rely on aluminum components for their lightweight and aesthetic appeal. Laser welding enables seamless integration of these parts.
4. Construction and Architecture
Architectural designs often utilize aluminum for its corrosion resistance. Laser welding creates strong, sleek joints for structural and decorative elements.
5. Renewable Energy
In the solar and wind energy sectors, aluminum frames and components benefit from the precision and reliability of laser welding.
Steps to Achieve Perfect Laser Welds in Aluminum
1. Surface Preparation
Before welding, the aluminum surface must be cleaned to remove oxides and contaminants. This step ensures better laser absorption and stronger welds.
2. Laser Selection
Choosing the right laser power and wavelength is crucial. Fiber lasers, for instance, are highly effective for aluminum due to their ability to handle high reflectivity.
3. Process Parameters
Adjusting settings such as laser power, focus, and welding speed ensures optimal results. These parameters vary based on material thickness and joint design.
4. Cooling and Solidification
Proper cooling prevents cracking and distortion as the weld solidifies, maintaining the structural integrity of the aluminum.
Innovations in Laser Welding Aluminum
AI Integration
Artificial intelligence is revolutionizing laser welding by enabling real-time monitoring and adjustments. AI ensures consistent quality and reduces operator dependency.
Hybrid Welding
Combining laser welding with traditional methods, such as TIG or MIG welding, enhances strength and versatility for specific applications.
Advanced Beam Technology
Innovations in beam shaping and delivery are further improving the precision and efficiency of laser welding aluminum.
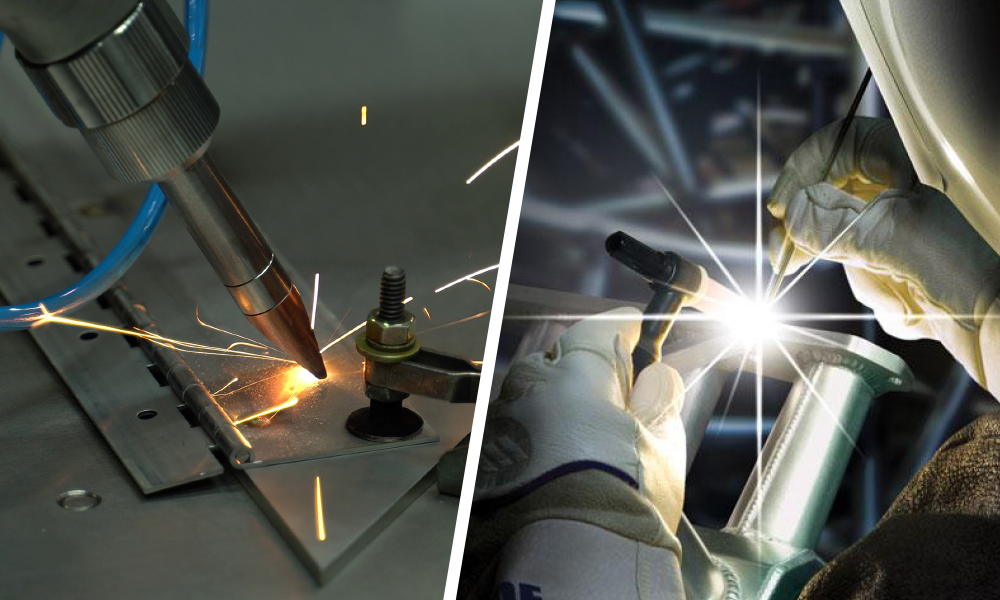
Economic and Environmental Impact of Laser Welding Aluminum
1. Cost Efficiency
While the initial investment in laser welding equipment may be high, the long-term savings in labor, materials, and energy outweigh the costs.
2. Sustainability
Laser welding aligns with green manufacturing practices by minimizing waste and reducing energy consumption.
3. Reduced Scrap Rates
The precision of laser welding minimizes errors, leading to less material wastage.
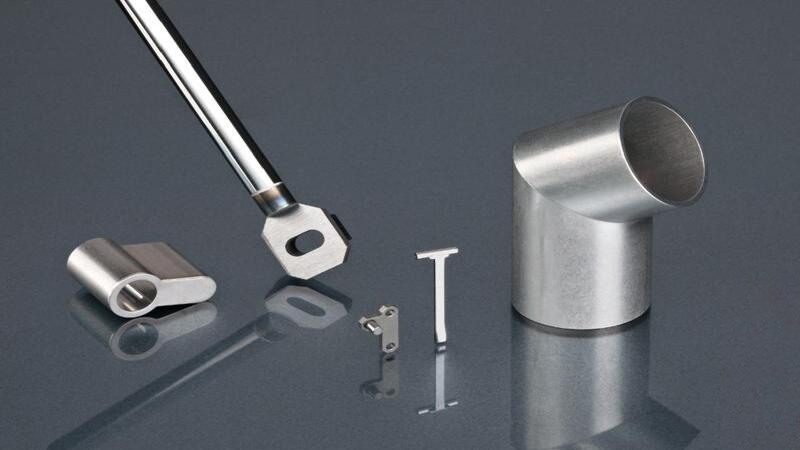
Safety Considerations
Laser welding involves high-intensity beams, necessitating strict safety protocols:
• Protective Eyewear: Operators must wear laser-rated glasses to shield their eyes.
• Ventilation Systems: Proper ventilation is essential to prevent exposure to harmful fumes.
• Training and Certification: Operators should undergo thorough training to ensure safe and effective operation of laser welding equipment.
Future Trends in Laser Weld Aluminum
Miniaturization of Equipment
Compact and portable laser welding systems are making this technology more accessible for small-scale businesses and fieldwork.
Energy Efficiency Enhancements
Advances in laser diode technology are driving down energy consumption while improving performance.
Automation and Robotics
Integration with robotic systems allows for automated welding, boosting productivity and reducing labor costs.
Final Thoughts
Laser weld aluminum is more than a technological innovation; it’s a practical solution to modern manufacturing challenges. Its ability to deliver precision, efficiency, and versatility makes it a cornerstone technique in industries worldwide. Whether you’re crafting intricate components or assembling large structures, laser welding aluminum empowers you to achieve flawless results.
Explore the potential of this cutting-edge method and unlock new possibilities in your projects. With laser welding, the future of aluminum fabrication is here.