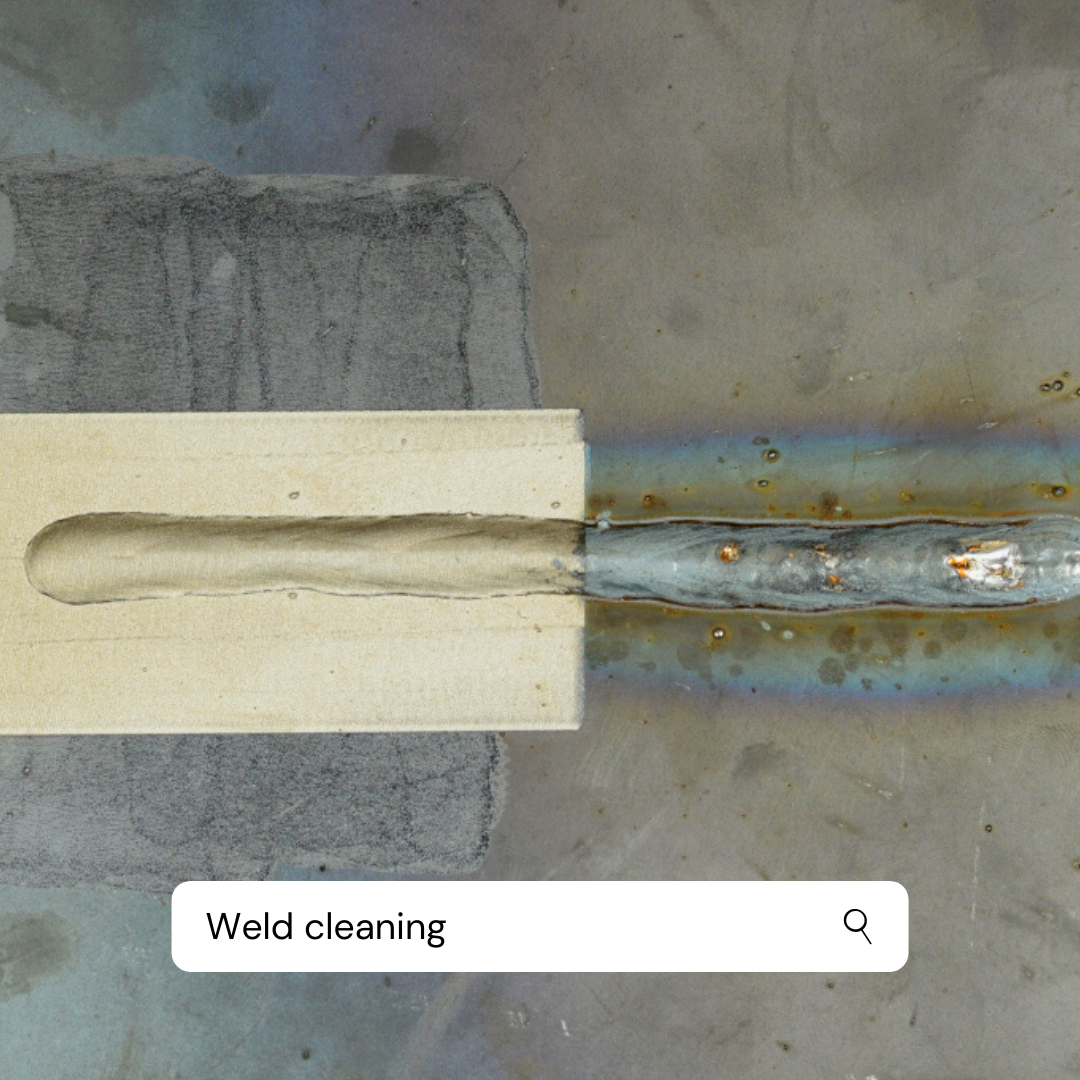
Laser Parts Cleaner: The Ultimate Solution for Industrial Component Cleaning
Introduction: Redefining Precision Cleaning with Laser Technology
Rust, grease, paint residues, and industrial contaminants—traditional cleaning methods struggle with precision, efficiency, and environmental impact. Whether it’s automotive parts, aerospace components, or delicate electronic surfaces, conventional techniques like chemical baths, abrasive blasting, and ultrasonic cleaning often cause damage or require extensive maintenance.
Enter the laser parts cleaner, a breakthrough in non-contact, eco-friendly surface treatment. This advanced system uses high-intensity laser pulses to remove contaminants without harming the base material, offering a safer, faster, and cost-effective alternative.
But how does laser cleaning technology work? What industries benefit the most? And is investing in a laser parts cleaner worth it? This in-depth guide explores its technology, applications, pricing, and long-term benefits to help you make an informed decision.
1. What is a Laser Parts Cleaner?
A laser parts cleaner is a specialized machine that removes surface contaminants using focused laser beams. Unlike traditional methods that rely on abrasives, solvents, or mechanical scrubbing, laser cleaning is a dry, contact-free, and environmentally friendly process.
How Does Laser Parts Cleaning Work?
1. A high-energy laser beam is directed at the contaminated surface.
2. The contaminants absorb the laser energy, causing them to break down or evaporate.
3. The underlying material remains untouched, as the laser selectively removes only the impurities.
4. The residue is expelled as fine dustor removed via a vacuum system.
This precision cleaning method ensures that delicate or high-value parts are cleaned without wear, chemical exposure, or deformation.
2. Why Choose a Laser Parts Cleaner Over Traditional Cleaning Methods?
Industries are rapidly shifting to laser cleaning technology for several reasons:
1. Non-Abrasive & Surface-Safe
• Unlike sandblasting or grinding, laser cleaning does not damage the substrate.
• Ideal for high-precision parts, including medical devices and aerospace components.
2.Chemical-Free & Eco-Friendly
• No solvents, acids, or cleaning agents
• Reduces hazardous waste disposal costs.
3. High Precision & Selective Cleaning
• Targets only the contaminants, preserving coatings and finishes.
• Ensures no material loss, making it perfect for delicate electronics and automotive parts.
4. Low Maintenance & Cost-Effective
• No consumables such as abrasives or chemicals.
• Minimal maintenancecompared to ultrasonic and chemical cleaning tanks.
5. Fast & Efficient
• Removes contaminants in seconds to minutes.
• Suitable for high-speed industrial applications.
With these benefits, laser cleaning outperforms traditional methods in terms of efficiency, safety, and long-term cost savings.
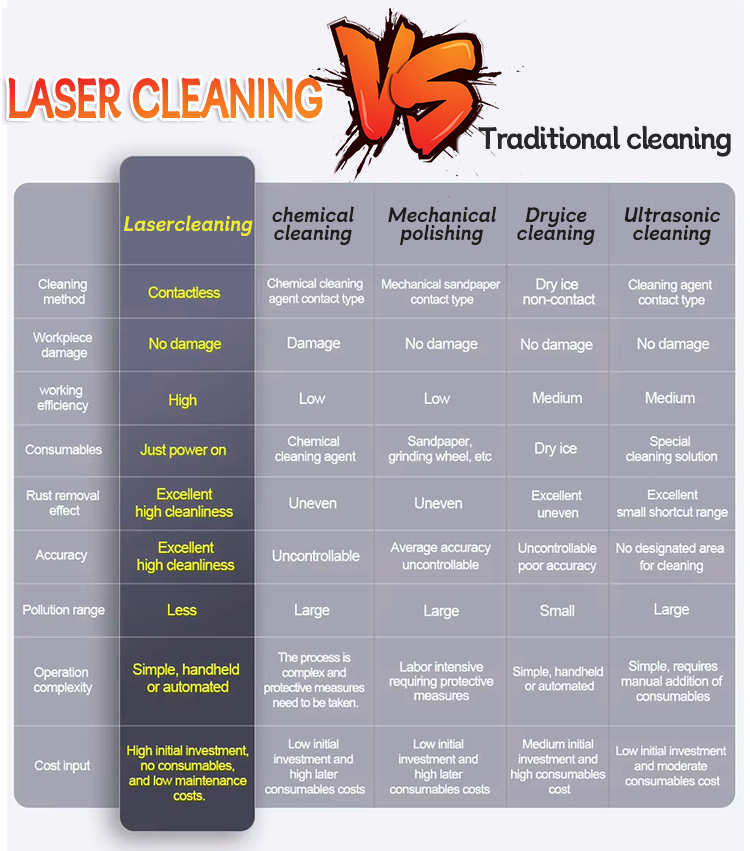
3. Key Applications of Laser Parts Cleaners
From automotive manufacturing to semiconductor production, laser cleaning technology is used in a variety of industries:
Automotive & Aerospace Industry
• Cleans engine components, fuel injectors, and transmission parts.
• Removes carbon deposits from turbine blades and aviation parts.
Electronics & Semiconductor Manufacturing
• Cleans printed circuit boards (PCBs) and microelectronics.
• Removes thin oxide layers from high-precision electronic components.
Medical Device Sterilization
• Cleans surgical instruments and high-precision medical implants.
• Ensures non-contaminated, residue-free surfaces.
Industrial Machinery & Metal Fabrication
• Removes grease, rust, and paint from manufacturing equipment.
• Prepares metal surfaces for welding, coating, or bonding.
Energy & Power Generation
• Cleans nuclear power plant components without radioactive contamination risks.
• Removes carbon buildup in wind turbine and solar panel structures.
By offering damage-free, high-precision cleaning, laser technology is rapidly becoming the preferred choice across industries.
4. How Much Does a Laser Parts Cleaner Cost?
The price of a laser parts cleaner depends on power, automation, and cooling systems.
Price Breakdown by Power Level
Power Output | Price Range (USD) | Best Use Cases |
---|---|---|
50W – 100W | $3,000 – $10,000 | Small parts, electronics, light-duty cleaning |
200W – 300W | $10,000 – $30,000 | Automotive, industrial, and general manufacturing |
500W – 1000W | $30,000 – $70,000 | Aerospace, heavy-duty cleaning, turbine parts |
1500W+ | $70,000+ | Large-scale industrial applications |
Factors Influencing Cost
1. Laser Type:Fiber lasers are more durable and efficient than CO2 lasers.
2. Cooling System:Water-cooled systems support longer cleaning cycles.
3. Automation & AI Features:Smart laser systems improve efficiency but increase cost.
4. Handheld vs. Robotic:Handheld models are more affordable, while fully automated units cost more.
Despite the initial investment, the long-term savings in maintenance and labor costs make laser cleaning technology a cost-effective solution.
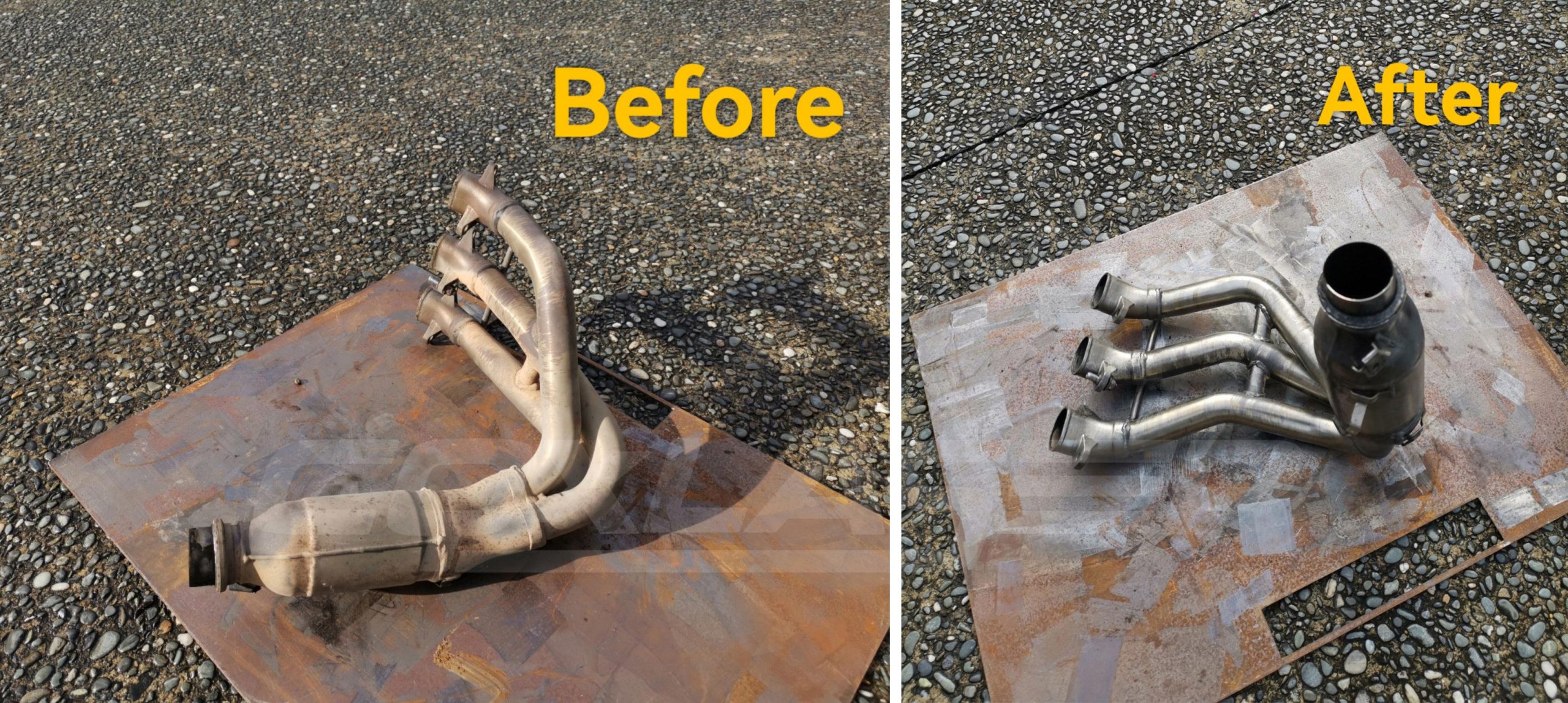
5. The Long-Term Savings & ROI of a Laser Parts Cleaner
1. Eliminates Consumable Costs
• No need for chemical solvents, abrasive materials, or cleaning agents.
• Reduces waste management costs.
2. Low Labor & Maintenance Costs
• Faster cleaning reduces manual labor time.
• No complex moving parts, leading to minimal downtime.
3. Increases Equipment Lifespan
• Prevents corrosion and material degradation.
• Maintains original part dimensions without wear.
4. Compliance with Environmental Standards
• Meets global green manufacturing regulations.
• Reduces toxic waste production and workplace hazards.
For companies looking to streamline operations, cut costs, and meet sustainability goals, laser cleaning offers unmatched long-term benefits.
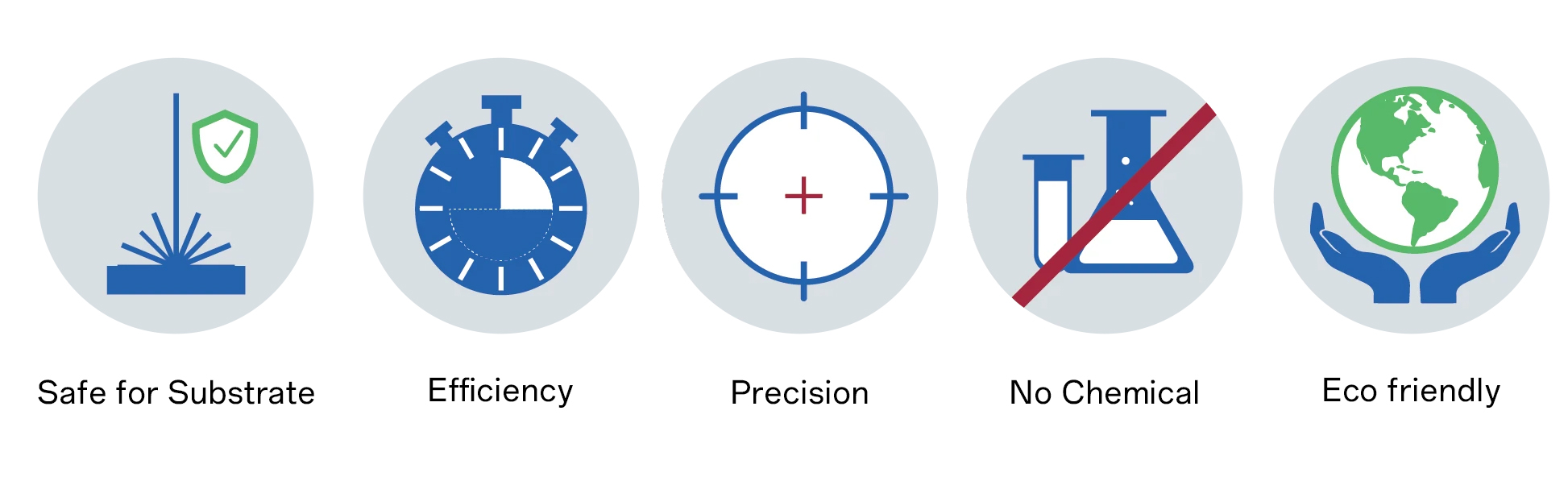
6. Choosing the Right Laser Parts Cleaner for Your Needs
Before investing in a laser cleaning system, consider:
1. Power Requirements:
° 50W – 100W:For small electronics and delicate parts.
° 200W – 300W:Best for industrial maintenance and automotive components.
° 500W+:Ideal for heavy-duty cleaning and aerospace applications.
2.Portability vs. Fixed Installations:
° Handheld models for flexibility.
° Automated systems for production-line cleaning.
3.Cooling Mechanism:
° Air-cooled for light-duty tasks.
° Water-cooled for industrial and high-power use.
4.Budget vs. Performance:
° Higher investment often means greater long-term ROI.
By selecting the right power level, automation features, and cooling system, businesses can maximize efficiency and cost-effectiveness.
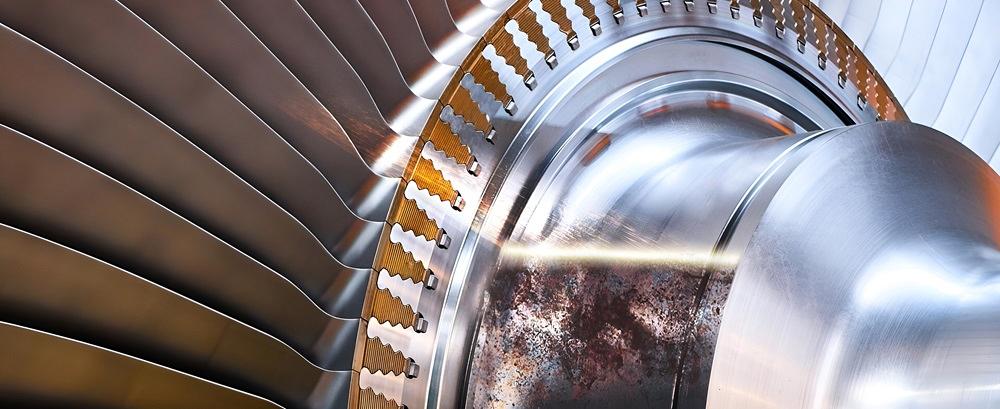
Final Thoughts: The Future of Laser Cleaning Technology
A laser parts cleaner is more than just an advanced cleaning tool—it’s an investment in efficiency, sustainability, and precision. As laser technology evolves, we can expect faster processing speeds, improved energy efficiency, and increased affordability.
With industries prioritizing eco-friendly solutions and automation, laser cleaning systems will continue to reshape industrial maintenance, precision manufacturing, and restoration processes worldwide.