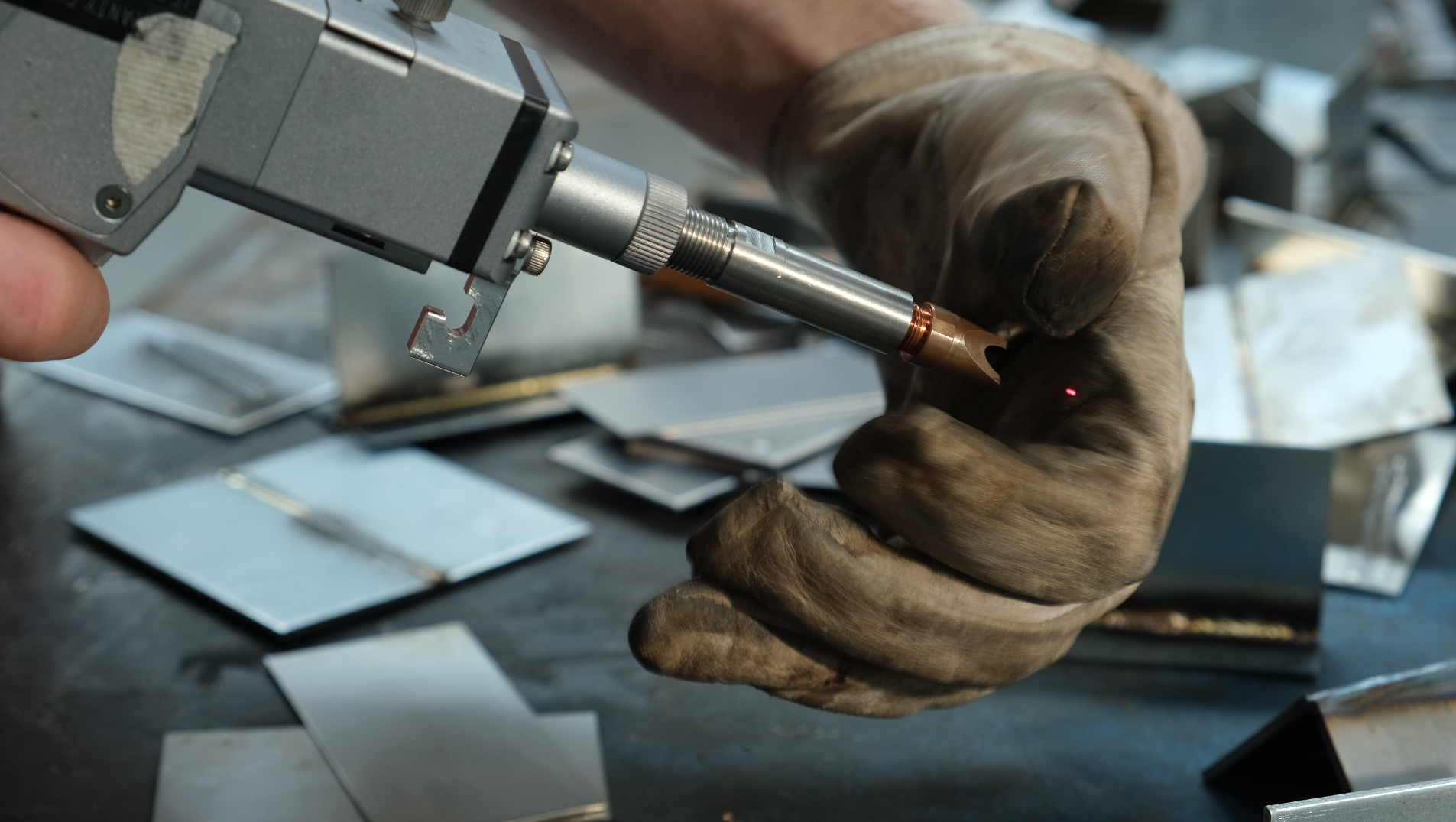
Is Laser Welding Strong? Exploring Unmatched Bonding Strength
Is laser welding strong enough to handle demanding industrial applications? The answer is an emphatic yes. Laser welding delivers a level of precision, strength, and durability that surpasses traditional welding methods. Picture two metal components fused seamlessly with minimal heat-affected zones and a bond so robust that it can withstand extreme forces. This is the power of laser welding—a tool trusted in industries where reliability is paramount, such as aerospace, automotive, and medical device manufacturing.
In this guide, we’ll dive deep into the strength of laser welding, examine its working principles, and compare it with conventional welding methods.
1. How Strong is Laser Welding?
Laser welding creates a high-strength joint by using a concentrated energy beam to melt the edges of materials and fuse them together. The result is a seamless weld that can rival or even exceed the strength of the base material when executed correctly.
Key factors that contribute to the strength of laser welds include:
1. Precise Energy Distribution:Ensures consistent weld depth and minimal thermal distortion.
2. Minimal Defects:Reduced porosity and microcracks due to the controlled environment.
3. Weld Penetration:Depending on the power settings, laser welding can penetrate deep into materials, creating robust bonds.
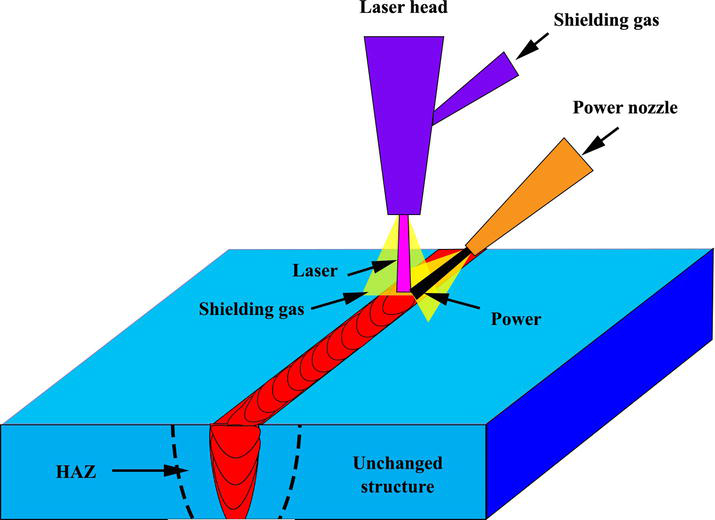
2. The Science Behind the Strength of Laser Welding
The strength of laser welding lies in its ability to create a clean, controlled molten pool with rapid cooling. Here’s how it works:
1. Energy Concentration:The fiber or solid-state laser directs a high-energy beam at a specific point.
2. Melting Process:The material absorbs the energy, melting the edges without excessive heat spread.
3. Fusion and Solidification:As the material cools, it solidifies into a uniform, defect-free joint.
The minimal heat-affected zone (HAZ) reduces stress in the surrounding material, preventing warping or cracking that weakens traditional welds.
3. Comparing Laser Welding Strength to Other Methods
Welding Method | Tensile Strength | Heat-Affected Zone | Post-Processing | Defect Rate |
---|---|---|---|---|
MIG Welding | Moderate | Large | High | High |
TIG Welding | High | Medium | Moderate | Moderate |
Laser Welding | Very High | Minimal | Minimal | Low |
Laser welding provides superior tensile strength and maintains material integrity better than MIG and TIG welding due to its precise control over heat input and fusion depth.
4. Factors Affecting the Strength of Laser Welds
Several factors influence the strength of laser welds:
4.1 Power Output
Higher wattage increases the penetration depth, creating stronger welds for thicker materials.
4.2 Beam Focus
A narrow, well-focused beam concentrates energy more effectively, enhancing weld quality.
4.3 Material Type
Metals like stainless steel and titanium respond exceptionally well to laser welding, forming strong bonds without impurities.
4.4 Joint Design
Proper joint alignment and preparation improve weld strength by ensuring uniform heat distribution.
5. Common Applications Where Laser Welding Strength is Essential
5.1 Aerospace Engineering
Laser welding joins critical components that must endure extreme pressure and temperature changes without failure.
5.2 Automotive Industry
High-strength welds are crucial for assembling car frames, engine components, and exhaust systems.
5.3 Medical Device Manufacturing
Laser welds create strong, sterile seams in surgical tools, implants, and diagnostic equipment.
5.4 Electronics Manufacturing
Laser welding provides secure, precise connections for microchips, sensors, and circuit boards.
6. Key Benefits of Strong Laser Welds
6.1 High Joint Strength
Laser-welded joints are often as strong or stronger than the base material.
6.2 Consistent Quality
Automated laser welding ensures uniform welds with minimal variation, crucial for mass production.
6.3 Enhanced Durability
The lack of defects, such as porosity and cracks, enhances the longevity and reliability of laser-welded structures.
6.4 Minimal Thermal Distortion
Laser welding’s precise heat input reduces the risk of material warping or weakening.
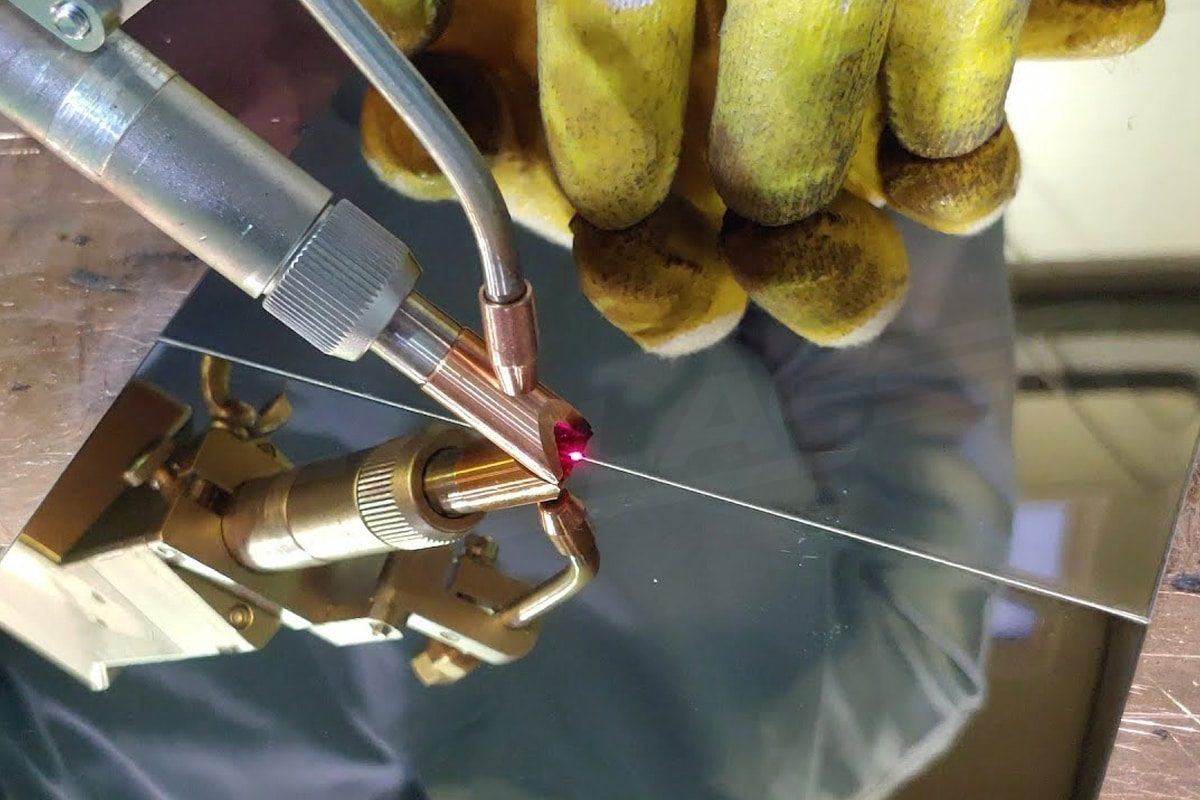
7. Real-World Case Studies: Laser Welding Strength in Action
7.1 Aerospace Components
A leading aerospace manufacturer implemented laser welding for turbine blade assembly. The result was a 30% increase in part strength and a significant reduction in weight compared to traditional riveting.
7.2 Automotive Frame Assembly
An automotive plant integrated robotic laser welding for chassis construction, leading to a 40% improvement in crash resistance and a 20% faster production time.
8. Comparing Laser Weld Joint Types and Their Strengths
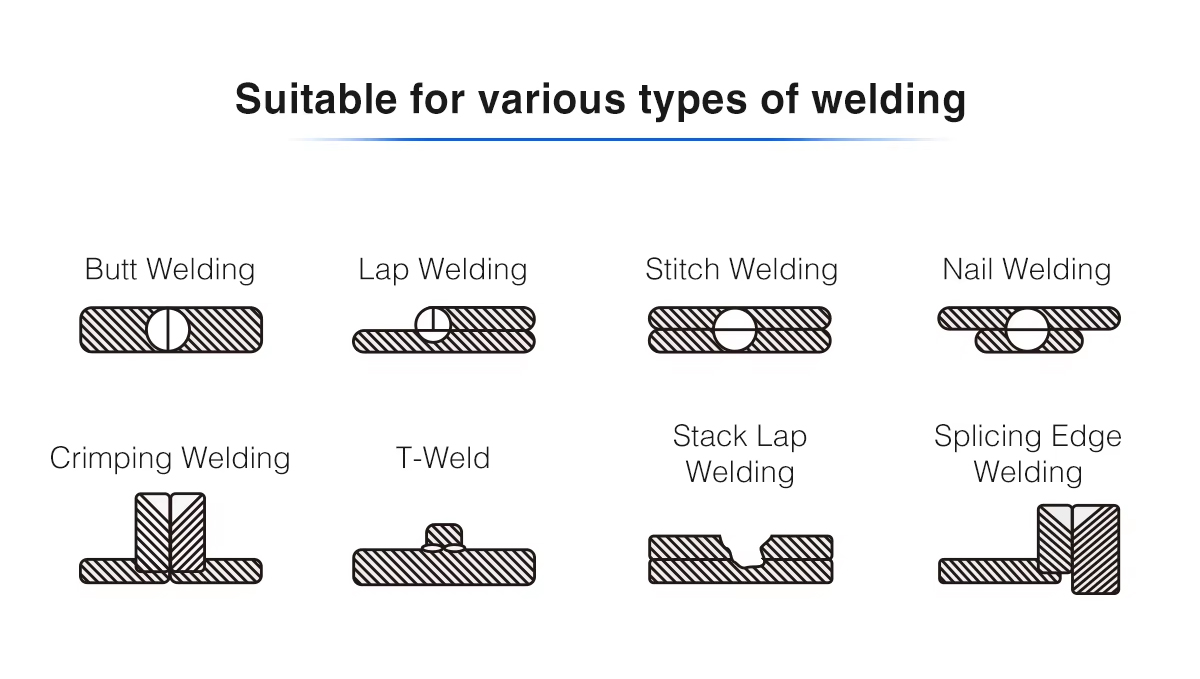
Joint Type | Description | Relative Strength | Common Use Cases |
---|---|---|---|
Butt Joint | Edges of two plates joined end-to-end. | High | Aerospace, automotive frames |
Lap Joint | One plate overlaps another. | Medium | Sheet metal, enclosures |
T-Joint | Perpendicular joint between two pieces. | High | Structural components |
Corner Joint | Two plates meet at a right angle. | High | Frames and casings |
9. Enhancing Laser Weld Strength: Best Practices
9.1 Optimize Power Settings
Adjust the power to suit the material thickness and joint type for optimal penetration.
9.2 Pre-Clean the Materials
Remove dirt, grease, and oxide layers to prevent contamination and ensure a strong weld.
9.3 Use Protective Gas
Shielding gases, such as argon, prevent oxidation and maintain weld purity.
9.4 Regular Maintenance
Clean and inspect the focusing optics and cooling system to maintain consistent performance.
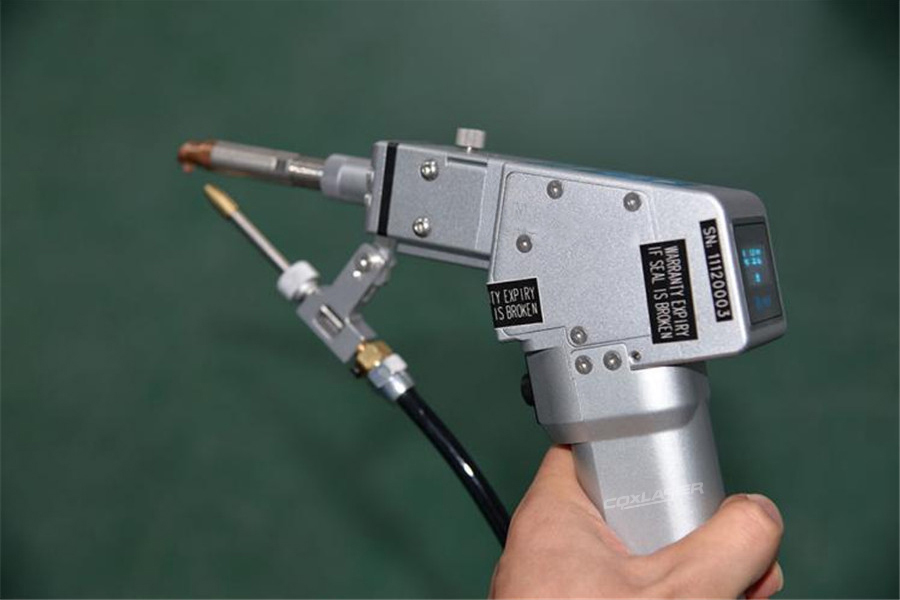
10. Addressing Common Misconceptions About Laser Weld Strength
• “Laser welds are too brittle”:Laser welds can be just as ductile as traditional welds if the correct settings are used.
• “Laser welding only works for thin materials”:High-power machines can weld thick metals with exceptional strength.
11. Innovations in Laser Welding Strength
11.1 AI-Powered Weld Optimization
Artificial intelligence systems analyze and adjust weld parameters in real time, ensuring maximum strength.
11.2 Multi-Beam Welding
Newer systems use multiple laser beams to increase fusion depth and joint strength.
11.3 Advanced Metal Alloys
Research into laser-compatible alloys is expanding the range of materials that can achieve high-strength welds.
12. FAQs About Laser Welding Strength
Q: How strong is a laser weld compared to a TIG weld?
A: Laser welds can achieve comparable or greater tensile strength, depending on the material and settings.
Q: Can laser welding be used for structural components?
A: Yes, many industries use laser welding for critical load-bearing components due to its high joint strength.
Q: Do laser welds require post-processing?
A: In most cases, laser welds have smooth finishes that require little to no post-processing.
Laser welding proves its strength across industries by delivering consistent, high-performance welds that withstand extreme conditions. By understanding its working principles and optimizing settings, manufacturers can harness the full potential of this revolutionary welding technology.