One solution to expand the application field of laser welding in industrial production and promote the industrialization of laser welding is to use laser wire welding. Laser wire welding can weld butt plates and thick plates with large gaps. It can also adjust the chemical composition of the weld when connecting dissimilar metals, and has a significant effect on suppressing thermal cracks after welding. Aluminum alloy is a very common metal in the aviation, aerospace and automotive industries, but aluminum alloy has a large reflectivity to lasers, the joints soften, and thermal cracks are easily generated during the welding process. These problems limit the application of high-power laser welding technology in the aluminum alloy processing industry. The use of filler materials can increase the absorption rate of aluminum alloys and stabilize the welding process. For some aluminum alloys that are prone to solidification cracks, the use of filler materials prevents crack formation.

The filling of welding wire makes the laser welding process more complicated. Mastering the wire feeding characteristics of laser wire welding under different welding conditions is a prerequisite for obtaining high-quality welds.
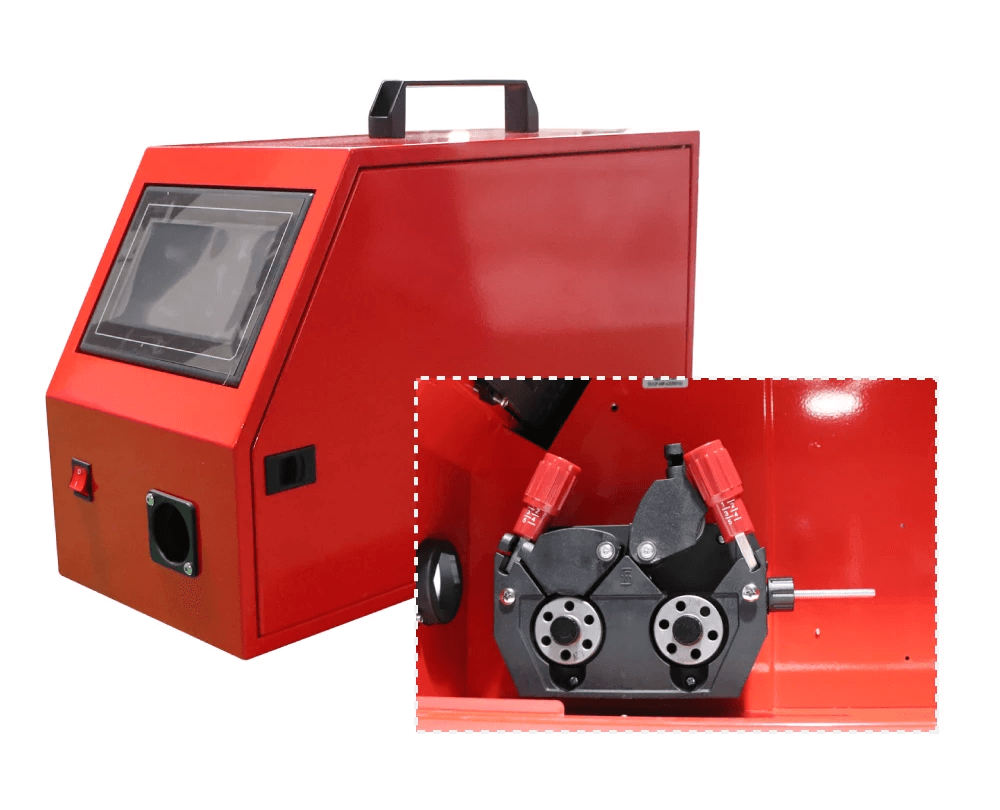
Wire feeding speed is an important process parameter of laser wire welding. Reasonable selection of wire feeding speed can make full use of laser energy and improve production efficiency. The wire speed should be determined according to the gap amount of the joint. If the wire feeding speed is too fast or too slow, it will cause the accumulation or lack of wire droplets in the transition to the molten pool, and it will also affect the interaction between the laser and the welding wire and the base material, thereby affecting the formation of the weld. The wire feeder equipped with the CQX Laser laser welding machine can keep the set wire feeding speed unchanged during the welding process.