
Industrial Laser Cleaning: The Future of Surface Treatment
Introduction: Why Industrial Laser Cleaning is Transforming the Industry
Dirt, rust, grease, and coatings—traditional cleaning methods have long relied on abrasive blasting, chemical treatments, or manual scrubbing. These processes are not only time-consuming but also generate hazardous waste and cause surface damage. Now, a revolution is underway: industrial laser cleaning.
Harnessing the power of high-intensity laser beams, this advanced cleaning technology is redefining efficiency and sustainability across industries. From manufacturing to automotive restoration, laser cleaning provides precise, non-contact, and eco-friendly solutions for removing contaminants without harming underlying materials.
How does this technology work? What are its applications? And most importantly, why are businesses rapidly adopting it? Let’s explore the world of industrial laser cleaning and see how it is shaping the future of surface treatment.
1. What is Industrial Laser Cleaning?
Industrial laser cleaning is a cutting-edge technique that utilizes laser pulses to remove unwanted materials from a surface. Unlike traditional methods that rely on abrasion or chemical solvents, laser cleaning offers a controlled, non-invasive way to eliminate contaminants such as rust, paint, oxide layers, and grease.
How It Works:
1. A high-energy laser beam is directed at the target surface.
2. The contaminant layer absorbs the laser energy and is vaporized or broken into fine particles.
3. The residue is then removed by suction, air blowers, or natural dispersion.
Key Advantages:
• Non-contact process:No mechanical force is applied to the surface.
• Selective cleaning:Only the unwanted layer is removed, preserving the base material.
• Eco-friendly:Eliminates the need for hazardous chemicals.
• Minimal waste:No additional cleaning materials required.
• Automation-ready:Can be integrated into robotic systems for high-speed industrial use.
2. Key Applications of Industrial Laser Cleaning
Laser cleaning is revolutionizing various industries by offering cost-effective, damage-free solutions. Here are some of the most impactful applications:
Manufacturing & Metal Processing
• Removal of oxidation layersbefore welding or painting
• Cleaning machinery partsfor precision maintenance
• Degreasing metal surfacesin automotive and aerospace industries
Automotive Restoration & Maintenance
• Rust and paint removal from vehicle frames
• Cleaning engine componentswithout dismantling
• Preparing surfaces for coating or adhesive bonding
Aerospace & Defense
• Removal of carbon depositsfrom jet engine components
• Surface preparation for spacecraft and aircraft parts
• Maintenance of military equipment with non-abrasive methods
Electronics & Semiconductor Industry
• Precision cleaning of circuit boardsand microelectronics
• Removing thin oxide layerswithout damaging sensitive components
• Cleaning high-value materials like gold and platinum contacts
Cultural Heritage & Conservation
• Restoration of historical monuments and artifacts
• Cleaning delicate paintings and sculptures
• Removing soot and dirtfrom stone surfaces without abrasion
Oil & Gas Industry
• Cleaning drilling equipment and pipelines
• Removing corrosion and contaminantsfrom metal structures
• Maintenance of offshore platformswithout shutting down operations
The versatility of laser cleaning makes it an invaluable tool across multiple industries, improving efficiency while reducing environmental impact.
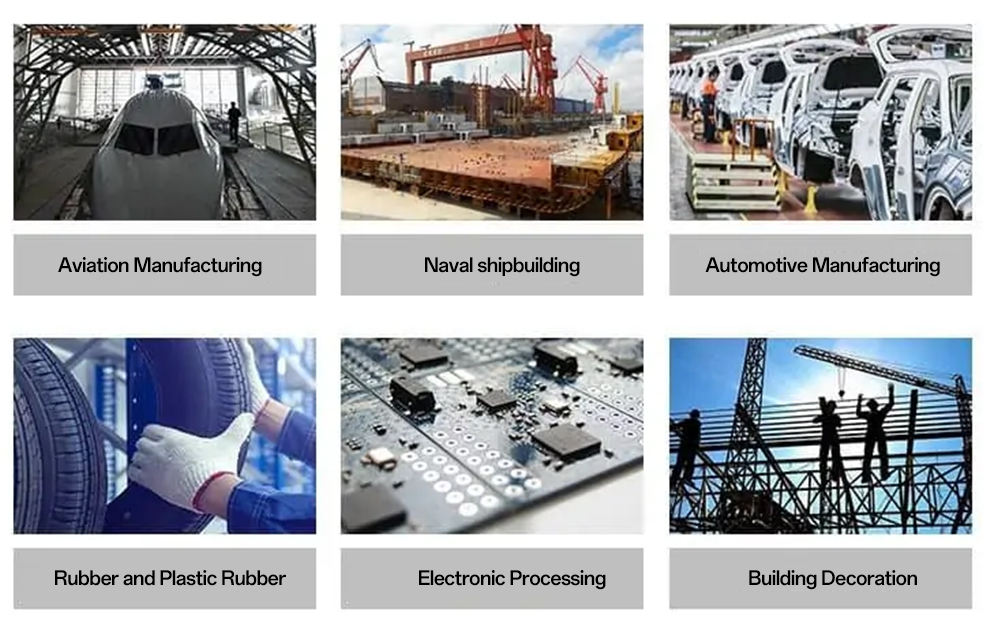
3. Why Businesses are Adopting Industrial Laser Cleaning
The shift towards industrial laser cleaning is driven by several compelling benefits:
1. Cost-Effective in the Long Run
While initial investments in laser cleaning equipment may seem high, businesses benefit from reduced maintenance costs, lower labor requirements, and elimination of chemical expenses.
2. Environmentally Sustainable
Unlike sandblasting or chemical stripping, laser cleaning produces no toxic waste and consumes minimal energy, aligning with global sustainability efforts.
3. Improved Workplace Safety
Traditional methods expose workers to hazardous chemicals and abrasive particles. Laser cleaning minimizes health risks and enhances workplace safety standards.
4. Precision & Non-Destructive Cleaning
Laser technology enables selective material removal, ensuring delicate surfaces remain undamaged while contaminants are effectively eliminated.
5. Faster Cleaning & Reduced Downtime
Laser cleaning significantly reduces downtime in industrial production, allowing businesses to maintain productivity while ensuring equipment cleanliness.
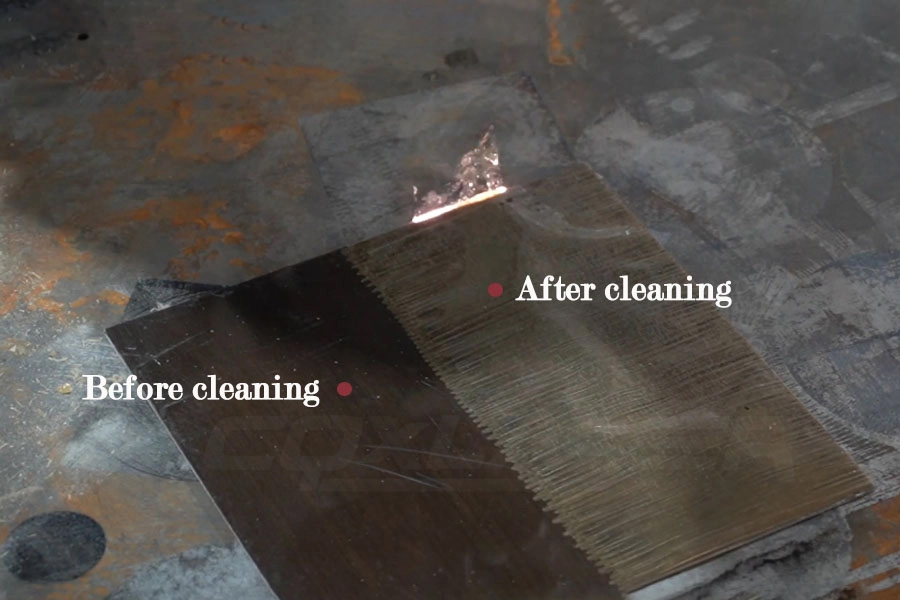
4. How to Choose the Right Industrial Laser Cleaning System
Selecting the best industrial laser cleaning system requires understanding key specifications and matching them with application needs.
1. Power & Pulse Type
• Low-Power (50W – 100W):Suitable for delicate cleaning applications like electronics and artwork.
• Mid-Power (200W – 500W):Ideal for automotive restoration and machinery maintenance.
• High-Power (1000W+):Used in heavy industrial applications such as shipbuilding and aerospace.
2. Portability vs. Fixed Installations
• Handheld laser cleanersare great for on-site maintenance and flexibility.
• Automated laser cleaning systemsare integrated into production lines for large-scale industrial cleaning.
3. Cooling Mechanism
• Air-cooled systemsare compact but may not support high-power lasers.
• Water-cooled systemsprovide better performance for extended industrial use.
4. Safety Features & Compliance
Ensure the laser system complies with industry safety standards, including protective enclosures, fume extraction, and user-friendly controls.
5. Future Trends in Industrial Laser Cleaning
As industries push towards automation and sustainability, the future of industrial laser cleaning is promising.
1. AI & Machine Learning Integration
• Smart sensors will auto-adjust laser parametersbased on material type.
• AI-powered robots will perform self-guided cleaningin industrial environments.
2. Increased Accessibility & Affordability
• Advancements in fiber laser technologywill lower equipment costs.
• More compact, portable designswill make laser cleaning accessible to small businesses.
3. Higher Efficiency & Energy Optimization
• Next-gen lasers will feature higher pulse frequenciesfor faster cleaning.
• Improved energy efficiencywill further reduce operational costs.
Industrial laser cleaning is not just a trend—it is a transformative shift in surface treatment technology. Businesses that adopt laser cleaning today position themselves for sustainability, efficiency, and long-term cost savings.
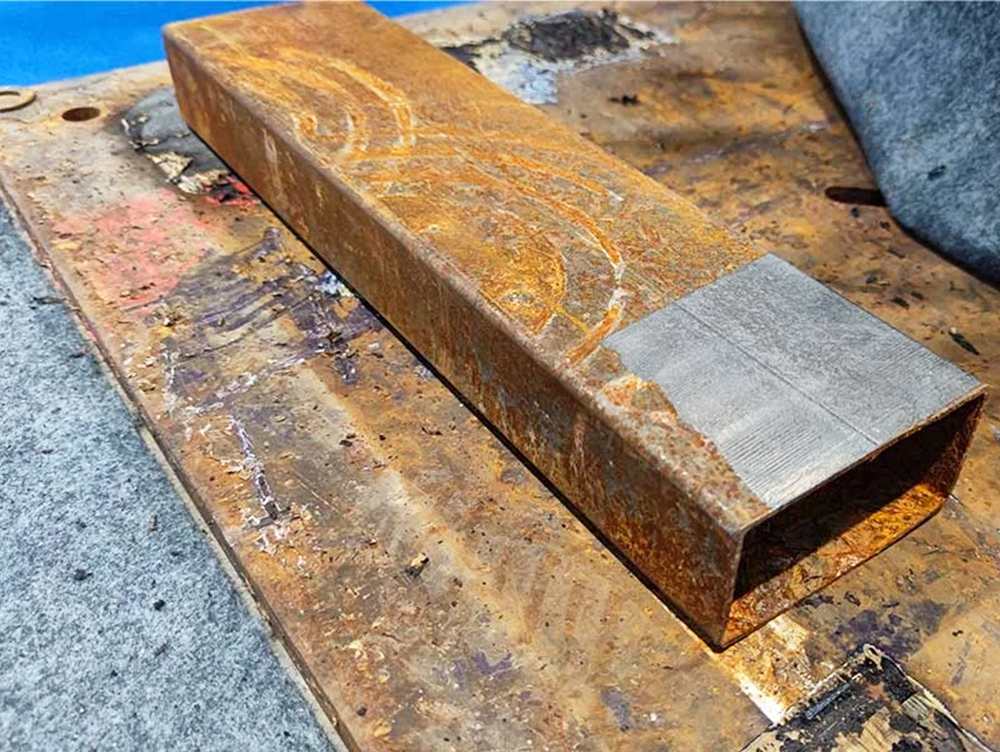
Final Thoughts: The Future of Industrial Surface Cleaning
Industrial laser cleaning is setting new standards for efficiency, safety, and environmental responsibility. Whether for automotive, aerospace, or manufacturing, laser cleaning provides precise, eco-friendly, and cost-effective solutions for modern industries.
As laser technology evolves, businesses will continue to benefit from faster processing times, reduced maintenance costs, and superior cleaning results. Now is the time to explore how industrial laser cleaning can optimize your operations and drive long-term value.