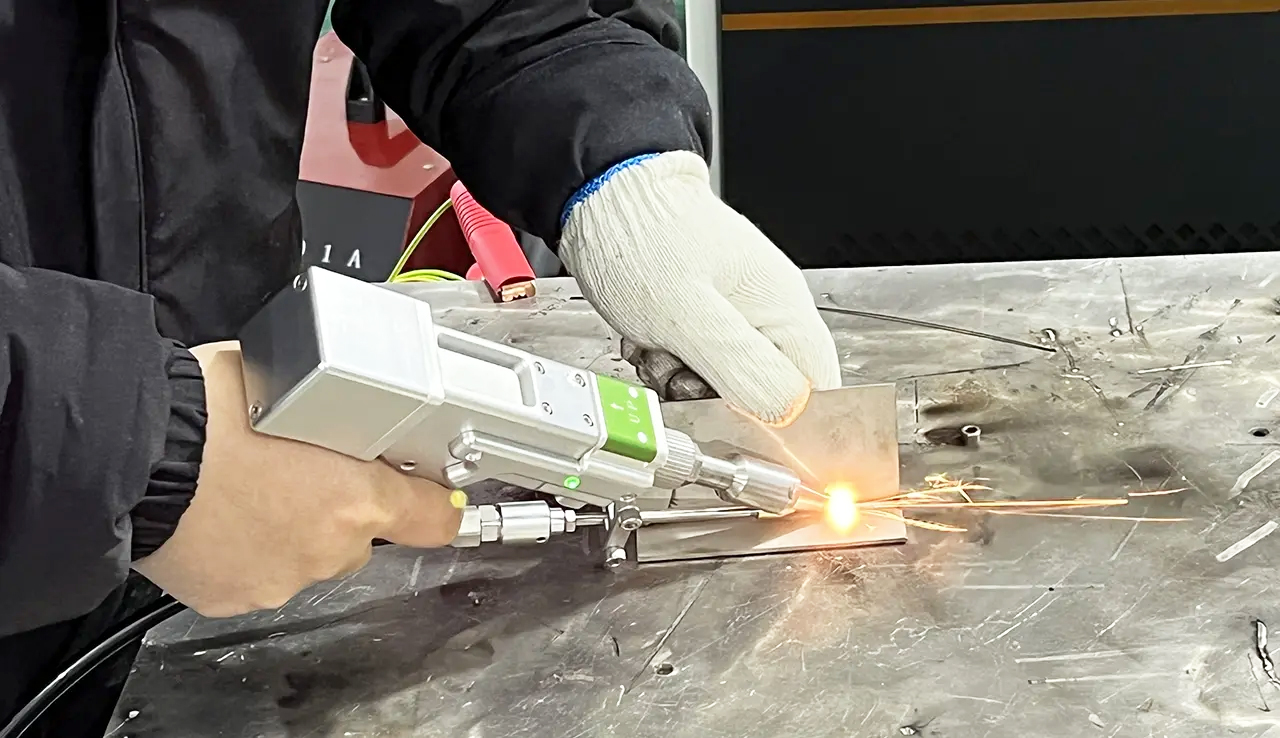
How Does Laser Welding Work: A Comprehensive Breakdown
How does laser welding work? The answer lies in a combination of science, precision, and cutting-edge technology. Picture a beam of light so focused and powerful that it melts metal instantly, bonding two pieces seamlessly. Unlike traditional welding methods that rely on extreme heat, contact, and fillers, laser welding uses a concentrated energy beam for unparalleled precision and minimal distortion.
In this guide, you’ll gain a detailed understanding of the laser welding process, its principles, techniques, advantages, and how it compares to traditional welding methods.
1. How Does Laser Welding Work?
Laser welding works by directing a focused beam of high-energy light onto a material’s surface, causing it to melt and bond. This process is contactless, relying on the heat generated by the laser to fuse the workpieces. Depending on the settings, laser welding can create either a shallow surface weld or a deep, narrow joint that penetrates through thick materials.
2. Components of a Laser Welding System
Understanding how laser welding works starts with knowing the core components of the system:
1. Laser Source:This is the core of the system, producing a powerful laser beam (commonly fiber, CO2, or solid-state lasers).
2. Focusing Optics:These lenses concentrate the laser into a precise, narrow beam for high-energy application.
3. Control Unit:Modern systems use software interfaces to adjust parameters such as beam intensity, duration, and movement.
4. Workstation:A stable platform where the materials are positioned for welding.
5. Cooling System:Prevents overheating by dissipating excess heat generated during the process.
3. The Laser Welding Process: Step-by-Step Explanation
3.1 Initial Setup
The operator sets up the materials and configures the welding parameters, including power, beam size, and speed.
3.2 Beam Activation
Once activated, the laser emits a high-energy beam that strikes the surface of the material.
3.3 Melting and Fusion
The intense heat causes the material to melt, forming a molten pool at the joint.
3.4 Cooling and Solidification
As the beam moves or stops, the molten pool cools rapidly, solidifying into a strong, uniform joint.
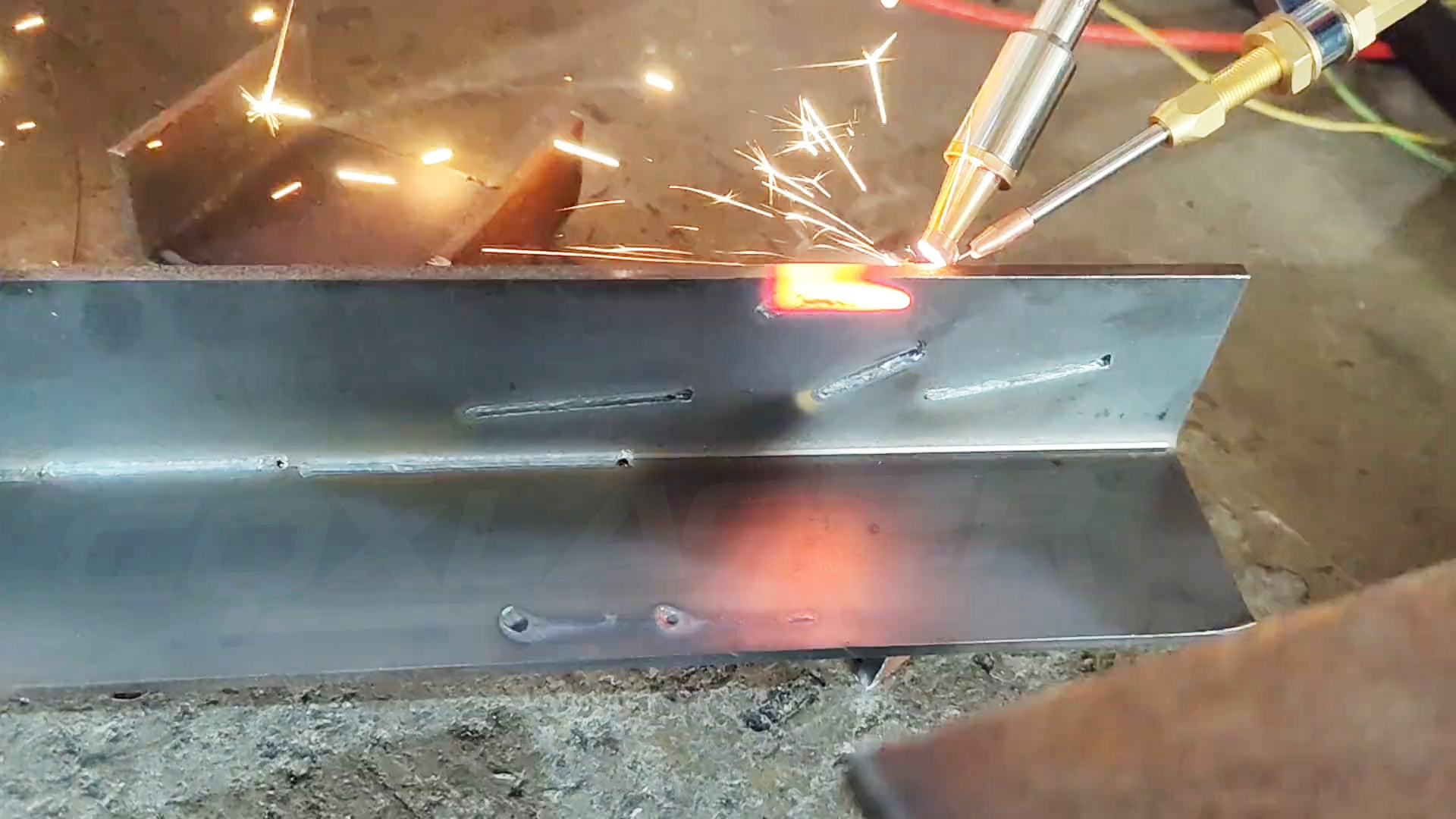
4. Types of Laser Welding Techniques
4.1 Keyhole Welding
This technique creates a deep, narrow weld by forming a small “keyhole” cavity within the material, allowing the laser to penetrate more deeply.
• Best For:Structural components, aerospace parts, and automotive frames.
4.2 Heat Conduction Welding
In this method, the laser heats the material surface without penetrating deeply. The result is a smooth, shallow weld that’s ideal for thin materials.
• Best For:Electronics, jewelry, and decorative seams.
4.3 Hybrid Laser Welding
Combining laser welding with other techniques, such as MIG or TIG welding, this method enhances weld strength and speed.
• Best For:Heavy-duty industrial applications.
5. Key Factors Affecting Laser Welding Performance
5.1 Power Output
Higher wattage lasers penetrate deeper and weld faster, making them suitable for thicker materials.
5.2 Beam Diameter
A narrower beam focuses energy more precisely, while a wider beam provides more surface coverage.
5.3 Welding Speed
Faster speeds can improve productivity but may reduce penetration depth and joint quality if not properly calibrated.
5.4 Material Type
Materials such as stainless steel, aluminum, and copper require different laser settings due to their varying reflectivity and conductivity.
6. Advantages of Laser Welding
6.1 High Precision
Laser welding excels at joining intricate parts with minimal distortion, making it perfect for delicate assemblies.
6.2 Minimal Heat-Affected Zone (HAZ)
By focusing energy precisely, the surrounding material remains unaffected, reducing the risk of warping and cracking.
6.3 Speed and Efficiency
Laser welding is significantly faster than traditional methods, enabling rapid production with consistent results.
6.4 Contactless Process
No physical contact means less wear on tools and fewer consumable costs.
6.5 Versatility
From thin wires to thick metal plates, laser welding accommodates a wide range of materials and thicknesses.
7. Common Applications of Laser Welding
7.1 Aerospace and Defense
Used to join lightweight yet durable components, ensuring precision without adding excess weight.
7.2 Medical Devices
Laser welding plays a vital role in producing surgical instruments, implants, and other medical equipment that demand high precision and cleanliness.
7.3 Jewelry and Watchmaking
Ideal for creating seamless joints in small, intricate designs without damaging delicate surfaces.
7.4 Automotive Manufacturing
Welds exhaust systems, chassis parts, and drivetrain components with consistent quality.
7.5 Electronics and Microfabrication
Laser welding is indispensable in the assembly of sensors, circuits, and battery enclosures.
8. Cost Considerations
Laser welding system costs vary widely based on the following factors:
• Laser Type:Fiber lasers tend to be more efficient but more expensive.
• Automation Level:Fully automated systems cost significantly more than manual or semi-automated ones.
• Power Output:High-power machines capable of deep welds cost more upfront but offer faster processing.
Typical Price Ranges:
• Entry-Level Systems:$10,000 – $30,000
• Industrial Systems:$50,000 – $500,000+
9. Safety Measures in Laser Welding
Despite being a precise and efficient process, laser welding requires proper safety precautions:
1. Laser Safety Goggles:Protect eyes from intense laser beams.
2. Ventilation Systems:Remove fumes generated during welding to maintain air quality.
3. Protective Enclosures:Shield the operator from stray beams and reflections.
10. Comparing Laser Welding to Traditional Methods
Welding Method | Precision | Speed | Heat-Affected Zone | Post-Processing |
---|---|---|---|---|
MIG Welding | Moderate | Moderate | Large | High |
TIG Welding | High | Slow | Medium | Moderate |
Laser Welding | Very High | Fast | Minimal | Minimal |
11. Emerging Trends in Laser Welding
• AI-Assisted Welding:Real-time optimization of weld parameters for improved accuracy and defect reduction.
• Portable Laser Welders:Compact, battery-operated models for fieldwork and remote applications.
• Eco-Friendly Technology:Energy-efficient laser sources designed to reduce power consumption.
12. FAQs About How Laser Welding Works
Q: Can laser welding be used for all metals?
A: Most metals, including steel, aluminum, and titanium, can be welded with a laser, though some materials require specific settings.
Q: Is laser welding faster than traditional welding?
A: Yes, laser welding can be up to four times faster due to its high processing speed and precision.
Q: How long does a laser welding machine last?
A: With proper maintenance, most laser welding machines have a lifespan of 10–15 years.
By understanding how laser welding works, you can appreciate its role in advancing modern manufacturing. This powerful, efficient process offers unmatched accuracy, making it an essential tool in industries ranging from aerospace to electronics. Whether you’re considering investing in a system or simply curious about the science behind the technology, laser welding represents the future of precision joining.