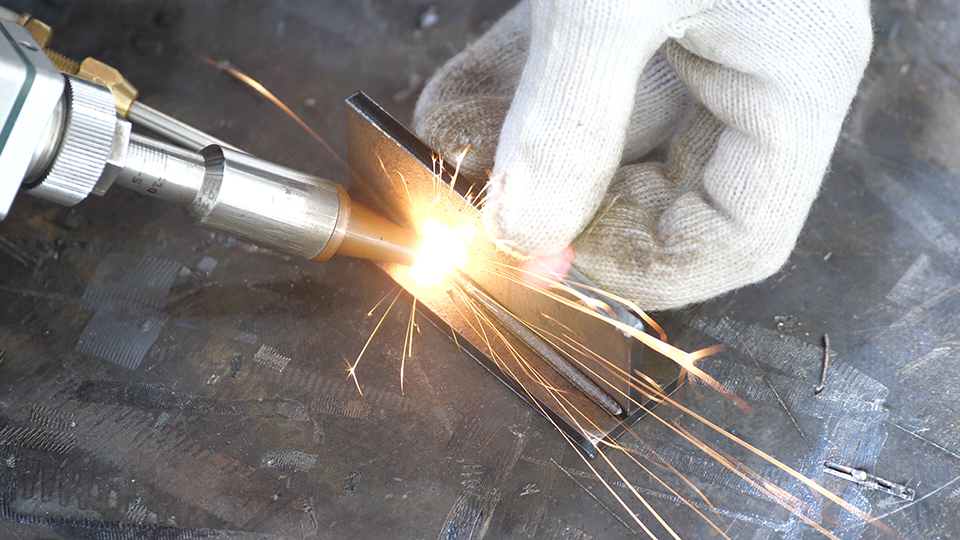
Unveiling the Handheld Laser Welder: A Compact Giant in Welding Technology
Imagine a tool so precise, so portable, and so versatile that it feels like holding the future in your hands. The handheld laser welder is not just a technological marvel; it’s a game-changer, breaking barriers in industries ranging from automotive to aerospace. For years, welding was synonymous with bulky equipment, slow processes, and limited precision. But with the advent of handheld laser welders, the welding world has been redefined. This comprehensive guide takes you through the intricacies of this transformative technology, its applications, benefits, and how CQX’s innovative solutions are setting new benchmarks.
1. What Is a Handheld Laser Welder?
1.1 Definition and Core Features
A handheld laser welder is a portable welding device that utilizes high-intensity laser beams to join materials with unmatched precision. Unlike traditional welding methods, it combines portability with
cutting-edge technology, making it an essential tool for modern manufacturers.
1.2 How It Differs from Traditional Welding
Portability: Traditional welding machines are often cumbersome, while handheld laser welders are compact and lightweight.
Precision: Laser technology ensures cleaner and more accurate welds.
Versatility: Suitable for diverse materials such as steel, aluminum, and even delicate alloys.
2. The Science Behind Handheld Laser Welding
2.1 How It Works
Handheld laser welders generate concentrated light energy, which melts the material at the weld point, fusing it together.
This process ensures minimal heat dispersion, reducing the risk of distortion or damage to surrounding areas.
2.2 Key Components of a Handheld Laser Welder
Laser Source: The core of the machine, generating the laser beam.
Control System: Allows precise adjustment of power and beam intensity.
Cooling System: Prevents overheating and ensures consistent performance.
3. Advantages of Using Handheld Laser Welders
3.1 Precision Welding on the Go
Handheld laser welders generate concentrated light energy, which melts the material at the weld point, fusing it together.
This process ensures minimal heat dispersion, reducing the risk of distortion or damage to surrounding areas.
3.2 Cost-Effective Solutions
While the initial investment may be significant, reduced material wastage and faster welding times make it cost-efficient in the long run.
3.3 Versatility Across Applications
From repairing machinery to creating artistic metalwork, handheld laser welders adapt to various tasks seamlessly.
3.4 Energy Efficiency
The targeted laser beam minimizes energy loss, making it an environmentally friendly choice.
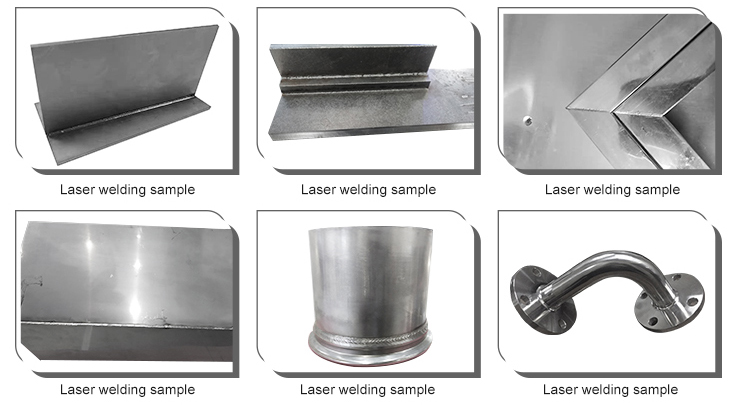
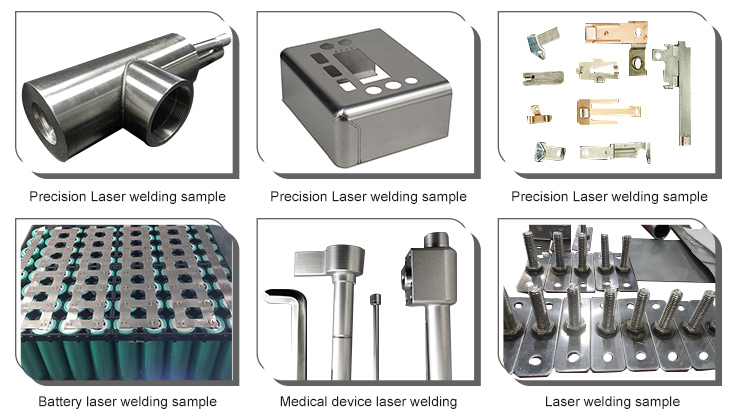
4. Applications of Handheld Laser Welders
4.1 Automotive Manufacturing
Used for welding thin sheets, car frames, and intricate components, handheld laser welders enhance the precision and strength of automotive parts.
4.2 Jewelry Design and Repair
The ability to weld delicate materials without distortion makes these welders perfect for high-end jewelry craftsmanship.
4.3 Aerospace Innovations
In aerospace, where precision is paramount, handheld laser welders are indispensable for creating lightweight and durable components.
4.4 Home Repair and DIY Projects
Their user-friendly design allows hobbyists and professionals to tackle a range of small-scale welding tasks.
5. How to Choose the Right Handheld Laser Welder
5.1 Assessing Your Needs
Consider the type of materials, the required welding depth, and the frequency of use.
5.2 Key Specifications to Look For
Power Output: Higher power ensures faster and deeper welds.
Portability: A lightweight and ergonomic design is crucial for handheld use.
Cooling System: Efficient cooling mechanisms extend the device’s lifespan.
5.3 Evaluating Suppliers
Choosing a reputable supplier like CQX ensures quality, reliability, and excellent customer support.
6. Maintenance Tips for Handheld Laser Welders
6.1 Daily Maintenance
– Inspect the lens for dust or debris. – Ensure the cooling system is functioning correctly.
6.2 Periodic Servicing
– Calibrate the laser beam to maintain precision. – Replace worn-out parts as needed.
6.3 Safety Precautions
– Always wear protective eyewear. – Operate in a well-ventilated space to avoid exposure to harmful fumes.
7. Innovations in Handheld Laser Welding
7.1 Integration with Automation
Modern handheld laser welders can be paired with robotic arms for semi-automated tasks, enhancing productivity.
7.2 Enhanced Beam Quality
Recent advancements have improved beam quality, allowing for finer and more precise welds.
7.3 User-Friendly Interfaces
Innovative designs now feature intuitive controls, making the technology accessible even to beginners.
8. Myths About Handheld Laser Welders
8.1 “They Are Too Expensive”
While the upfront cost might seem high, the long-term savings in efficiency and material costs justify the investment.
8.2 “Not Suitable for Heavy-Duty Tasks”
Handheld laser welders are capable of handling both delicate and robust welding tasks with ease.
8.3 “Difficult to Operate”
Modern handheld laser welders are designed for ease of use, with intuitive controls and ergonomic designs.
9. The Future of Handheld Laser Welding
9.1 Expanding Accessibility
With advancements in technology, handheld laser welders are becoming more affordable and widely available.
9.2 Eco-Friendly Solutions
As industries prioritize sustainability, the energy efficiency of handheld laser welders makes them a preferred choice.
9.3 New Materials and Applications
Ongoing research is expanding the range of materials that can be welded, opening new possibilities for innovation.
Handheld laser welders have redefined the standards of precision and portability in the welding industry. Their versatility, efficiency, and user-friendly designs make them indispensable tools for modern manufacturing. With CQX leading the charge in innovation, these welders are shaping the future of industrial and creative applications. By investing in a handheld laser welder, you’re not just upgrading your tools—you’re stepping into the future of welding technology.