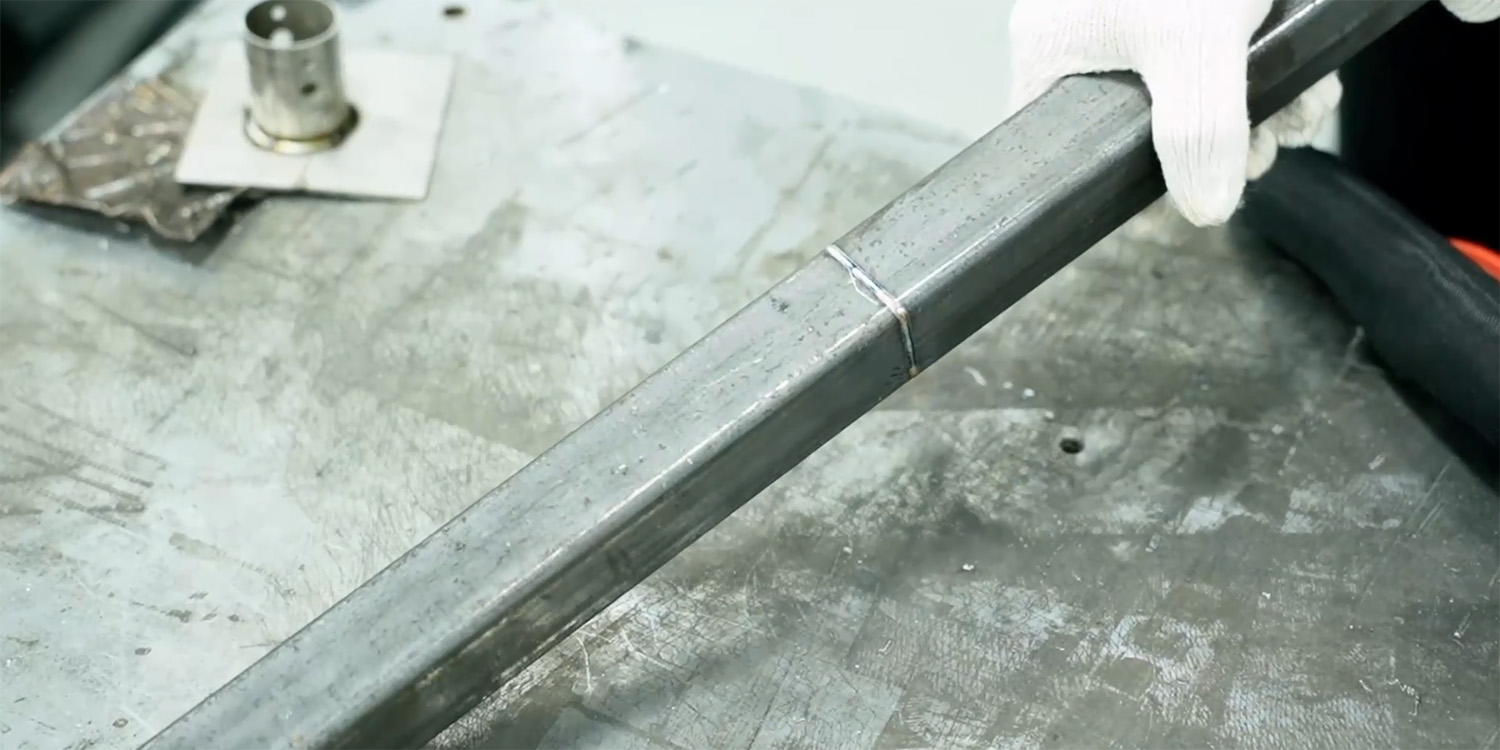
The Rise of Hand Laser Welding: Precision, Speed, and Versatility
When innovation meets practicality, the result is transformative. Hand laser welding represents the cutting edge of metalworking technology, bringing unparalleled precision, speed, and versatility to industries and individuals alike. From intricate repairs to large-scale manufacturing, this technique has redefined how metals are joined, offering consistent quality and impressive efficiency.
What Is Hand Laser Welding?
Hand laser welding uses a high-intensity, focused laser beam to fuse metal parts together. Unlike traditional welding methods, which often involve high heat and material distortion, laser welding provides targeted energy application. This results in clean, durable welds with minimal thermal impact on surrounding materials.
In laser welding, the wire feeder is also a key part.the wire also helps the welder maintain a consistent standoff and focus spot, while the wire feed governs the travel. Look at hand-held laser welding in action and you’ll notice the welder pulling the torch toward him. In reality, the welder isn’t “pulling” the torch but instead is just keeping the torch angle steady, parallel to the workpiece, as the feeding wire propels the torch toward him. The feeling is unique—again, very different from traditional arc processes, which is why experienced welders sometimes have trouble adapting.
Why Hand Laser Welding Matters
1. Precision Beyond Compare
Hand laser welding delivers pinpoint accuracy, allowing for intricate designs and complex geometries that are impossible with other methods.
2. Versatility in Application
This technology works seamlessly across various metals, including stainless steel, aluminum, copper, and even dissimilar materials.
3. Efficiency Redefined
Its speed and minimal post-weld processing reduce production times, making it ideal for industries where deadlines are critical.
4. Environmentally Friendly
Laser welding consumes less energy and generates less waste compared to traditional welding methods, aligning with sustainable practices.
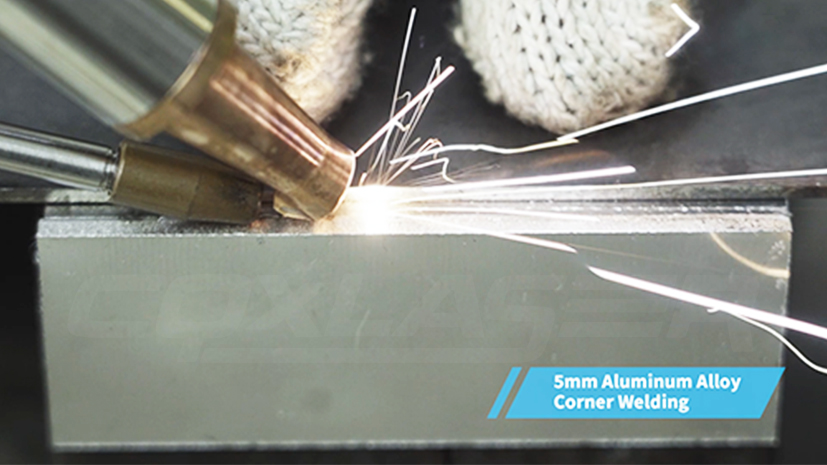
Core Features of Hand Laser Welding
Compact and User-Friendly Design
Handheld laser welders are ergonomically designed, making them easy to operate even for extended periods. This portability also enables on-site applications, eliminating the need for heavy machinery.
Minimal Heat Affected Zone (HAZ)
The focused nature of the laser minimizes heat spread, reducing material distortion and ensuring a cleaner weld.
High-Speed Operation
Laser welding is significantly faster than traditional methods, allowing for quicker project completion without sacrificing quality.
Seamless Integration with Automation
Many modern hand laser welders can be integrated into automated systems, combining human precision with robotic efficiency.
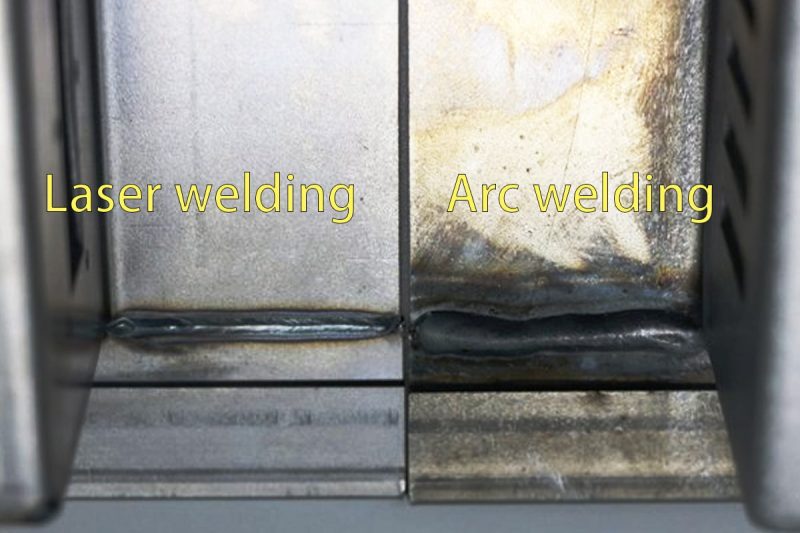
Applications of Hand Laser Welding
1. Automotive Industry
From intricate engine repairs to robust structural components, hand laser welding is a staple in automotive manufacturing and maintenance.
2. Aerospace Engineering
Precision and lightweight materials are critical in aerospace. Laser welding meets these demands, creating reliable components for high-stakes applications.
3. Jewelry Crafting
For artisans, laser welding offers the ability to create detailed designs and perform delicate repairs without damaging the material.
4. Medical Device Manufacturing
In an industry where accuracy and hygiene are paramount, laser welding provides clean, reliable results for surgical tools and implants.
5. Construction and Infrastructure
Laser welding streamlines the construction of metal frameworks and decorative elements, providing both strength and aesthetic appeal.
How Hand Laser Welding Works
1. Surface Preparation: The metal surfaces are cleaned to remove contaminants and ensure optimal laser absorption.
2. Laser Application: The focused laser melts the material at the joint, forming a molten pool.
3. Fusion: As the laser moves, the molten metal solidifies, creating a strong and seamless bond.
This process is efficient and adaptable, accommodating various material thicknesses and geometries.
Advantages Over Traditional Welding
Speed and Efficiency
Laser welding can complete tasks in a fraction of the time required by traditional methods, boosting overall productivity.
Enhanced Weld Quality
Its precision reduces the likelihood of defects, ensuring consistent and reliable results.
Lower Energy Consumption
The targeted nature of the laser minimizes energy waste, making it a cost-effective solution.
Reduced Material Waste
With minimal spatter and precise energy application, laser welding reduces waste and optimizes material usage.
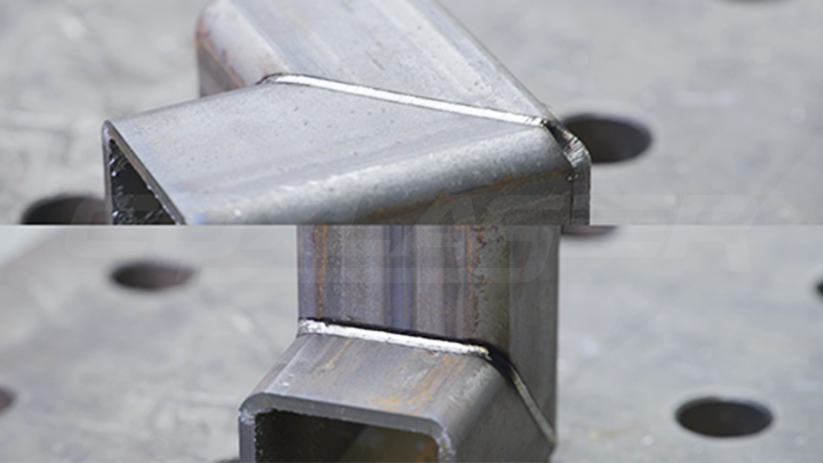
Choosing the Right Hand Laser Welding Equipment
Power Output
High-powered lasers allow for deeper penetration and faster operation, suitable for industrial applications.
Cooling Mechanism
Efficient cooling systems prevent overheating, ensuring prolonged operation and machine longevity.
Portability
Compact and lightweight designs enhance usability and flexibility, especially for on-site projects.
Safety Features
Integrated safety measures, such as protective shields and automatic shutoff systems, ensure user safety during operation.
Safety Considerations
Working with laser technology requires adherence to strict safety protocols:
• Wear appropriate protective eyewear to shield your eyes from laser exposure.
• Operate in a controlled environment to minimize the risk of accidents.
• Ensure proper ventilation to disperse any fumes generated during welding.
Economic and Environmental Impact
Cost-Effective Solution
While the initial investment in a hand laser welder may be significant, the long-term savings in labor, materials, and energy outweigh the upfront costs.
Sustainability
Laser welding’s reduced energy consumption and waste generation contribute to a more sustainable manufacturing process.
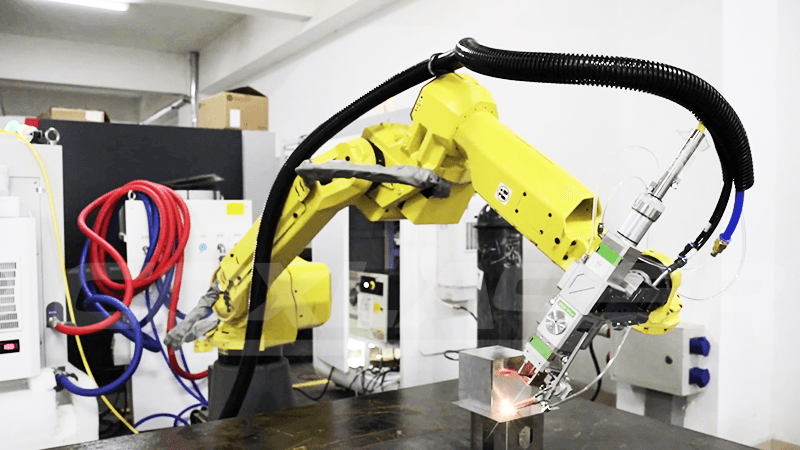
Future Trends in Hand Laser Welding
The field of hand laser welding is evolving rapidly, driven by technological advancements and industry demands. Emerging trends include:
1. AI Integration: Machines equipped with AI will adapt settings in real-time for optimal performance, reducing errors and downtime.
2. Enhanced Portability: Advances in materials and design will lead to lighter, more compact devices.
3. Improved Beam Quality: New laser technologies will increase precision and efficiency while reducing energy requirements.
Closing Thoughts
Hand laser welding is not just a tool; it’s a revolution in metalworking. Its combination of precision, speed, and versatility makes it an indispensable asset for professionals across various industries. Whether you’re crafting intricate jewelry or assembling industrial components, this technology empowers you to achieve unparalleled results.
Embrace the future of welding with hand laser technology and elevate your craft to new heights. The possibilities are endless, and the time to innovate is now.