Fiber Laser Welder: Transforming Welding with Precision and Efficiency
Imagine a welding tool so precise it could weld the most intricate designs, so efficient it could redefine manufacturing processes, and so versatile it could handle an array of materials—the fiber laser welder is not just an innovation; it’s a revolution in the welding world. Whether you’re a craftsman working on delicate jewelry or an industry titan constructing complex machinery, understanding the power of fiber laser welding can change the way you work. This guide explores every aspect of fiber laser welders, providing an in-depth look at their advantages, how they function, and why they are increasingly favored in modern manufacturing. We’ll also show you how CQX is leading the charge in delivering high-quality laser welding solutions.
1. What is a Fiber Laser Welder?
1.1 Overview of Fiber Laser Welding Technology
A fiber laser welder uses a fiber-optic cable to deliver a highly focused beam of laser light, generating intense heat that melts the material at the welding joint. This technique provides unmatched precision, ensuring that the welding process produces clean and strong bonds with minimal distortion.
1.2 Key Features of Fiber Laser Welders
• High Precision: The focused laser beam ensures extremely accurate welds, ideal for delicate and intricate work.
• Speed and Efficiency: Fiber lasers weld faster than traditional methods, reducing production time significantly.
• Versatility: Capable of welding various materials, including stainless steel, aluminum, copper, and even reflective metals that other lasers struggle with.
2.How Fiber Laser Welders Work
2.1 The Science Behind Fiber Laser Welding
Fiber laser welding works by concentrating high-power laser light into a small area, generating enough heat to melt and fuse materials. The laser is transmitted through a fiber-optic cable, allowing for precise energy delivery. This process minimizes the heat-affected zone (HAZ), which reduces the risk of material distortion and ensures the quality of the weld.
2.2 Key Components of a Fiber Laser Welder
• Laser Source: The core component, often a fiber laser, provides a high-quality, efficient light beam.
• Cooling System: Helps maintain optimal operating temperatures, ensuring consistent laser output.
• Control Interface: User-friendly systems for adjusting parameters like power, beam focus, and welding speed.
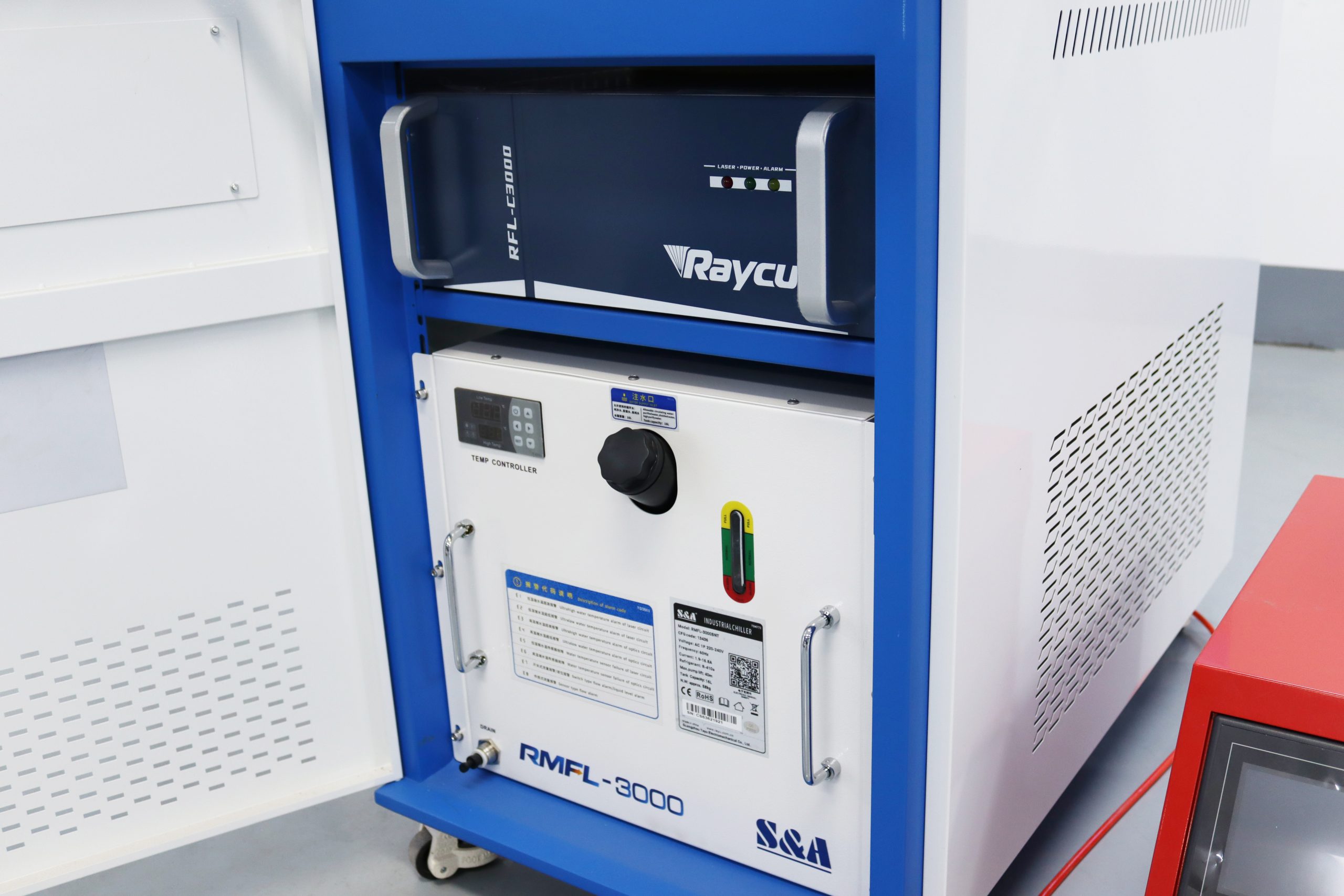
3. Advantages of Fiber Laser Welders
3.1 Precision and Quality
The precision of fiber laser welders is unparalleled, allowing users to create perfect welds with minimal error.
The high level of control reduces spatter, resulting in cleaner and aesthetically pleasing welds.
3.2 Increased Productivity
Fiber lasers are faster than traditional welding techniques, improving productivity.
The reduced production time means that manufacturers can meet tight deadlines without compromising on quality.
3.3 Versatility Across Industries
From automotive to medical device manufacturing, fiber laser welders are used in a wide range of industries due to their ability to handle different materials and thicknesses with ease. Their versatility makes them an ideal choice for manufacturers looking to improve efficiency.
3.4 Low Maintenance
Fiber lasers require less maintenance compared to other types of lasers.
The absence of moving parts in the laser source reduces wear and tear, making them a more cost-effective solution in the long run.
3.5 Energy Efficiency
Fiber lasers are more energy-efficient than other welding technologies.
Their efficiency results in lower energy costs, which is beneficial for high-volume production environments.
4. Applications of Fiber Laser Welders
4.1 Automotive Industry
Fiber laser welders are used in the automotive sector for welding car frames, exhaust systems, and other components that require precision and strength.
Their ability to handle both thick and thin materials makes them versatile tools in vehicle manufacturing.
4.2 Aerospace Manufacturing
In aerospace, where safety and precision are paramount, fiber laser welders are used to weld lightweight materials like aluminum and titanium, ensuring strong bonds without adding excess weight.
4.3 Medical Device Production
The medical industry relies on fiber laser welding for manufacturing devices like pacemakers, surgical tools, and implants.
The precision and cleanliness of the welds are critical to meeting the stringent standards required for medical devices.
4.4 Electronics and Microfabrication
For electronic components, fiber laser welders provide micro-welding capabilities that traditional welding cannot achieve.
They are ideal for welding tiny parts in circuit boards and sensors without damaging surrounding areas.
5. Key Considerations When Buying a Fiber Laser Welder
5.1 Power Output
The power of the laser affects the materials it can weld and the thickness it can handle. It is essential to choose a welder with the appropriate power level based on the intended applications.
5.2 Cooling Mechanism
Effective cooling is crucial to maintaining laser performance. Water-cooled systems are generally more effective than air-cooled options, especially for high-power lasers used in industrial applications.
5.3 Automation Features
Some fiber laser welders come with automation features like programmable settings, robotic integration, and remote control.
These features can significantly enhance productivity and consistency in high-volume production environments.
5.4 Safety Features
Safety is an important factor when working with laser welders. Look for features like enclosed workspaces, automatic shut-off, and protective eyewear to ensure safe operation.
5.5 Brand Reliability
Choosing a reputable brand like CQX ensures that you receive a high-quality product backed by robust customer support, training, and warranty services.
The reliability of the brand is a key factor in maximizing the value of your investment.
6. CQX Fiber Laser Welders: A Leader in Innovation
6.1 Advanced Technology
CQX fiber laser welders are equipped with the latest technology, providing users with efficient and precise welding solutions.
Features such as real-time monitoring and adaptive control ensure that every weld meets high-quality standards.
6.2 Robust Build Quality
The welders are designed for durability, using high-grade materials that can withstand the demands of industrial environments. CQX focuses on creating machines that are not only powerful but also resilient and long-lasting.
6.3 Comprehensive Customer Support
CQX offers training and ongoing support to help users maximize the potential of their fiber laser welders.
Their commitment to customer satisfaction ensures that businesses get the most out of their investment.
7. Fiber Laser Welding vs. Traditional Welding Methods
7.1 Heat Affected Zone (HAZ)
Fiber laser welding produces a much smaller heat-affected zone compared to traditional methods. This reduction in HAZ minimizes the risk of warping or weakening the material, which is especially important for sensitive applications.
7.2 Speed and Efficiency
Laser welding is significantly faster than MIG, TIG, or arc welding. The concentrated laser beam allows for rapid heating and cooling, speeding up the entire welding process and increasing throughput.
7.3 Material Compatibility
Unlike traditional welding, which may struggle with certain metals, fiber lasers can handle reflective and difficult-to-weld materials, such as aluminum and copper, with ease.

8. Future Trends in Fiber Laser Welding
8.1 Automation and Robotics
Automation is set to play a major role in the future of fiber laser welding. Robotic integration will enable precise and repeatable welds, making it easier to maintain quality in mass production environments.
8.2 AI and Machine Learning
AI and machine learning are being integrated into welding systems to help optimize weld parameters in real time, further enhancing precision and reducing defects.
8.3 Green Manufacturing
Fiber laser welding is already energy-efficient, but future developments aim to make it even more environmentally friendly. Improvements in energy use and the reduction of waste materials will make this technology a cornerstone of green manufacturing initiatives.
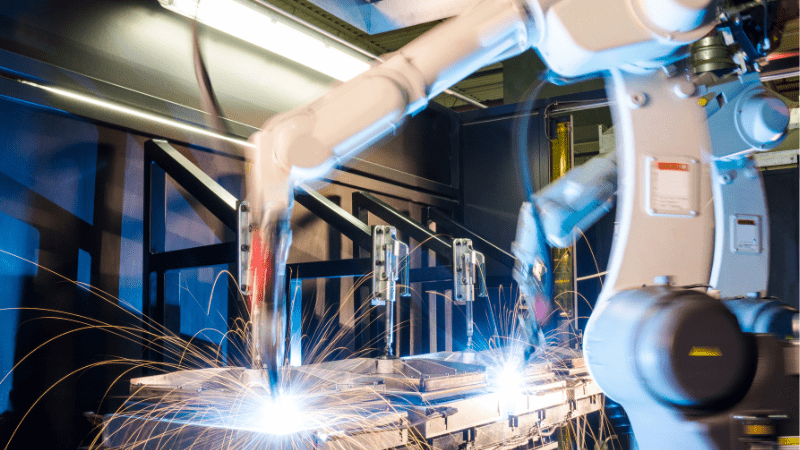
9. Tips for Choosing the Right Fiber Laser Welder
9.1 Assess Your Needs
Before selecting a fiber laser welder, assess the specific requirements of your projects. Consider factors like material type, thickness, production volume, and the level of precision needed.
9.2 Budget vs. Features
Determine your budget and compare it against the features offered by different models. Ensure that you are investing in a welder that provides the functionality you need without unnecessary extras that increase the cost.
9.3 Long-Term Value
Consider the long-term value, including maintenance costs, energy efficiency, and productivity gains. A higher initial investment in a CQX fiber laser welder can result in significant savings and performance improvements over time.
Fiber laser welders represent the pinnacle of welding technology, combining precision, speed, and versatility in one powerful package. Whether you’re working in automotive, aerospace, medical, or electronics industries, a fiber laser welder can greatly enhance your production capabilities. CQX is dedicated to providing high-quality fiber laser welders that meet the demands of modern manufacturing. By understanding the benefits, applications, and key considerations outlined in this guide, you can make an informed decision and take your welding operations to the next level.