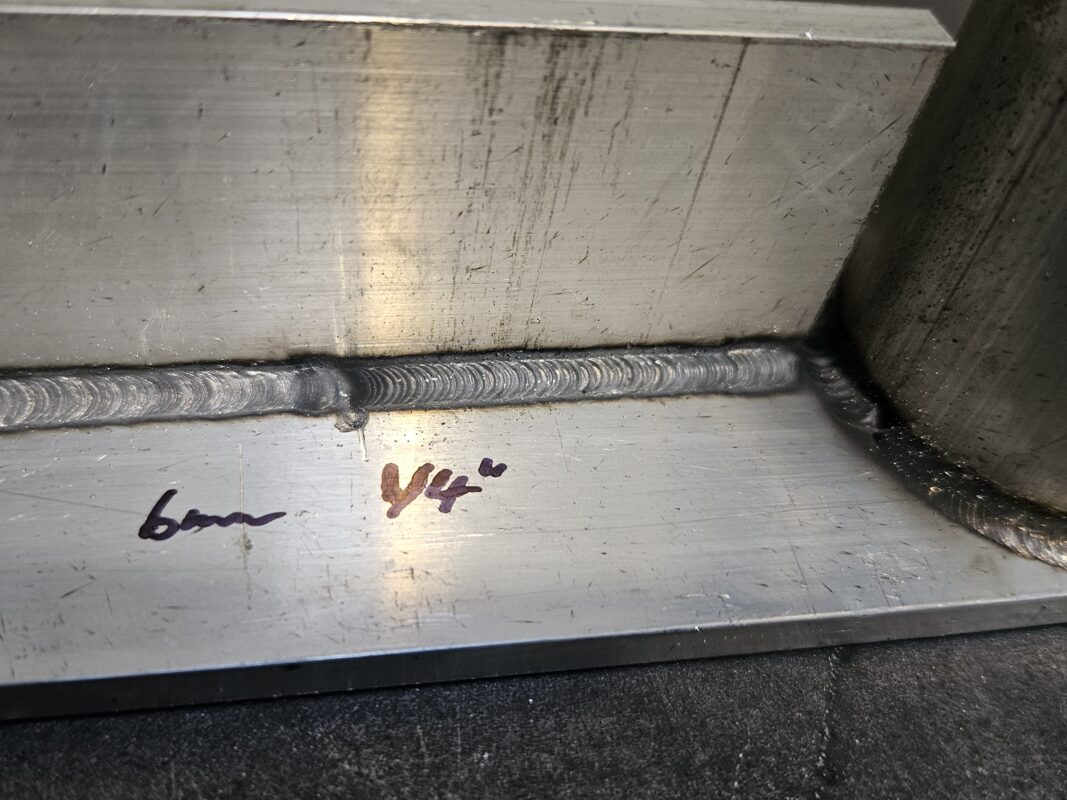
The Transformative Potential of an Aluminum Laser Welder
In the world of welding, precision isn’t a luxury—it’s a necessity. Enter the aluminum laser welder, a groundbreaking tool that redefines how aluminum is joined, offering unmatched efficiency, strength, and precision. Whether you’re a large-scale manufacturer or a craftsman, this technology holds the key to streamlined processes and impeccable results.
Understanding the Aluminum Laser Welder
An aluminum laser welder employs high-intensity laser beams to melt and fuse aluminum materials. Unlike traditional methods, laser welding ensures minimal distortion, higher weld quality, and faster production times. It is particularly suited for aluminum, a material known for its lightweight properties and excellent thermal conductivity.
Why Aluminum Needs Special Welding Techniques
Aluminum is a versatile material, but its properties pose challenges in welding:
1. High Thermal Conductivity: It dissipates heat quickly, making uniform heating essential.
2. Oxide Layer: The oxide layer on aluminum requires thorough cleaning to prevent weld defects.
3. Thermal Expansion: Its high expansion rate can cause distortion if improperly welded.
Laser welding overcomes these challenges with precision and localized heat application.
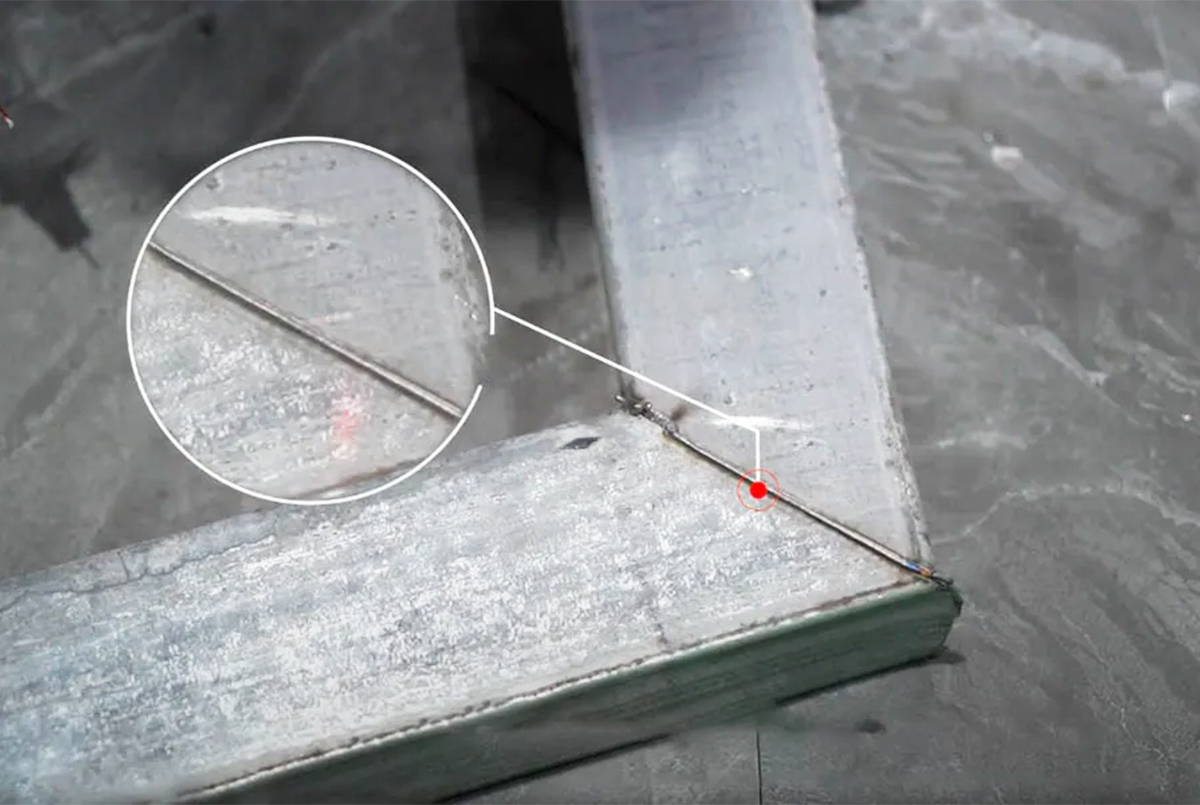
Benefits of Using an Aluminum Laser Welder
Superior Weld Quality
Laser welding produces clean, defect-free welds with minimal porosity. The high precision reduces spatter and ensures consistent results, even in high-stress applications.
Faster Production
The speed of laser welding outpaces traditional methods, allowing for quicker project completion. This efficiency is crucial in industries like automotive manufacturing, where time is money.
Reduced Post-Weld Processing
With its ability to produce smooth, polished welds, laser welding minimizes the need for grinding or polishing after the process.
Environmentally Friendly
Laser welding uses less energy than traditional methods and produces fewer emissions, aligning with sustainable industrial practices.
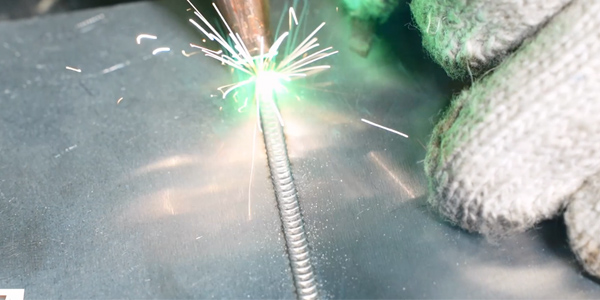
Applications Across Industries
Aerospace Engineering
In the aerospace sector, aluminum laser welders are invaluable for creating lightweight, high-strength components. The precision ensures the structural integrity required for critical applications.
Automotive Manufacturing
From chassis components to intricate engine parts, laser welding streamlines aluminum joining processes in automotive assembly lines.
Electronics and Semiconductors
Aluminum laser welders enable the precise joining of small, delicate components, crucial for electronics manufacturing.
Construction and Architecture
For aluminum frameworks, facades, and decorative elements, laser welding delivers seamless, aesthetically pleasing results.
Custom Fabrication and Prototyping
Craftsmen and small-scale manufacturers benefit from the flexibility and precision of laser welders for custom projects.
Choosing the Right Aluminum Laser Welder
Power Output
Higher wattage allows for deeper penetration and faster welding speeds, making it ideal for industrial applications.
Beam Quality
A high-quality laser beam ensures precision and consistent results, particularly for thin or intricate materials.
Cooling Systems
Efficient cooling prevents overheating, ensuring the machine operates at peak performance for extended periods.
Automation Features
Modern welders often include programmable settings and robotic integration, reducing manual effort and increasing accuracy.
How Aluminum Laser Welding Works
Step 1: Surface Preparation
The aluminum surface is cleaned to remove contaminants and the oxide layer, ensuring optimal laser absorption.
Step 2: Laser Application
A focused laser beam heats and melts the aluminum, creating a molten pool that fuses the materials.
Step 3: Solidification
As the laser moves away, the molten aluminum solidifies, forming a strong, durable weld.
This process occurs rapidly, with most welds completed in seconds, depending on material thickness and complexity.
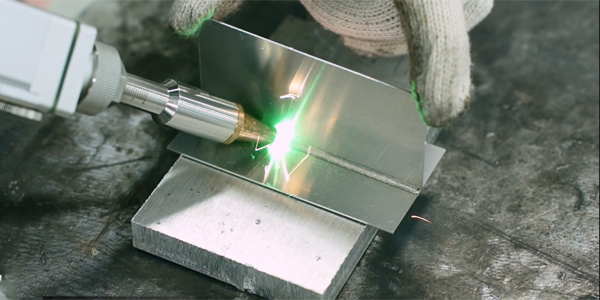
Safety Considerations
Laser welding involves high-intensity beams that require strict adherence to safety protocols:
• Use certified protective eyewear rated for the specific laser wavelength.
• Operate in a controlled environment to prevent accidental exposure to the laser.
• Ensure proper ventilation to avoid inhaling any fumes produced during welding.
Economic and Environmental Impact
Cost Efficiency
Although the initial investment in an aluminum laser welder may be higher, the long-term savings in time, labor, and material make it a cost-effective choice.
Sustainability
Laser welding’s reduced energy consumption and minimal material waste contribute to a greener manufacturing process.
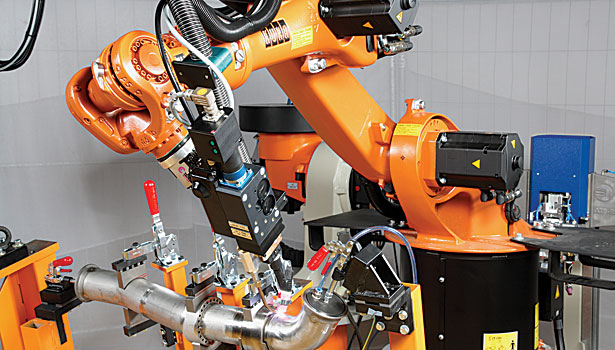
Future of Aluminum Laser Welding
As technology evolves, aluminum laser welding is expected to become even more efficient and versatile. Emerging trends include:
1. AI Integration: Machines will adapt in real-time, optimizing settings based on material properties and project requirements.
2. Portability: Compact, lightweight designs will make laser welders more accessible for field applications.
3. Enhanced Beam Technology: Advances in laser diodes and optics will improve precision and reduce energy consumption.
Final Thoughts
The aluminum laser welder is more than a tool—it’s a gateway to innovation. Whether you’re improving production efficiency or elevating craftsmanship, this technology offers the precision and reliability needed to meet modern demands. Embrace the future of welding today and unlock new possibilities with the power of lasers.